
Generalnie zawsze mnie kusiło totalnie i kompleksowo przerobić Hatsana. Oczywiście zamierzałem wykorzystać wszelkie sprawdzone i skuteczne patenty dotyczące tego karabinka mogące poprawić właściwości tego karabinka pod względem celności, kultury strzału oraz ilości oddanych strzałów z jednego ładowania kartusza.
Oczywiście chciałem dołożyć jakieś swoje patenty, a w dalszej perspektywie przerobić go na wersje BULLPUP :-D
Karabinek kupiłem od kolegi z forum. Jest to wersja 10 strzałowa z 5.5mm Lothar Walther.
Hatsan jak to hatsan nie powalał swoją kulturą pracy a i celność mogła by być lepsza.
Najwięcej czasu zajęło mi z wymiarowanie i zaprojektowanie detali potrzebnych do systemu bullpup i spustu. Wszystkie elementy narysowałem w AutoCad a następnie musiałem te rysunki przekonwertować na tryb maszynowy zrozumiały przez ploter frezujący CNC.
Określiłem zakres poprawek i przeróbek.
Etap I
-czyszczenie i mycie
-doprecyzowanie spustu, polerka detali, dorobienie elementów zwiększających zakres regulacji spustu
-poprawienie mechanizmu indeksowania magazynka
-poprawa korony wylotu lufy oraz portu ładowania
-centrowanie kanału dolotowego względem kanału w lufie
-szlifowanie i polerowanie popychacza śrutu, wymiana tulei prowadzącej popychacz
-odciążenie i polerowanie zbijaka
-szlifowanie i polerka końców sprężyny zbijaka
-wymiana śruby ograniczającej ruch zbijaka na tuleję gumową
-zrobienie centralnego otworu wylotowego z zaworu kartusza
-polerowanie kanału iglicy oraz iglicy
-wymiana wszystkich oringów
-założenie regulatora Andriusa
-smarowanie wszelkich elementów które tego wymagają
-znaczne zmniejszenie ilości zużywanego powietrza, potrzebnego do oddania 1-go strzału
Etap II
-zaprojektowanie mechanizmów oraz osady do systemu BULLPUP
-wykonanie wszelkich prowadnic cięgien i innych elementów
-wykonanie osady BULLPUP
-anodowanie elementów aluminiowych
-olejowanie osady
No to do dzieła

Etap I
Dobrze wszystkim znany mechanizm spustu rozebrany na części pierwsze. Wymieniłem wszystkie sprężynki na nowe bardziej miękkie.

Strzałka pokazuje luz między mechanizmami. Zlikwidowałem luzy za pomocą podkładek zrobionych z tworzywa PET.
Szlifowałem papierem wodnym 500 następnie 1000 oraz polerowałem, pasta+filc krzywki elementów spustu.
Zaprojektowałem i wykonałem za pomocą obrabiarki CNC jeden z elementów spustu, który pozwala na dowolna regulacje drugiego stopnia w spuście (wcześniej takiej regulacji nie było) śruba nr1 :-D
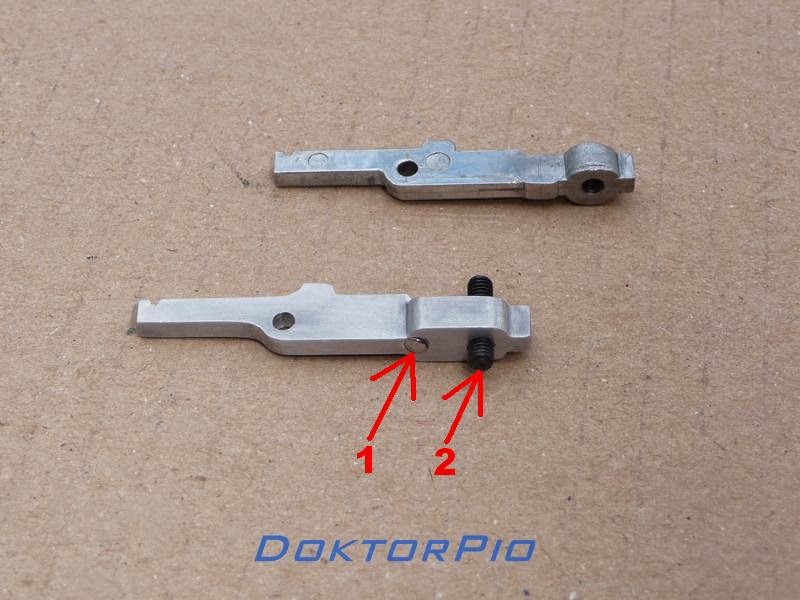
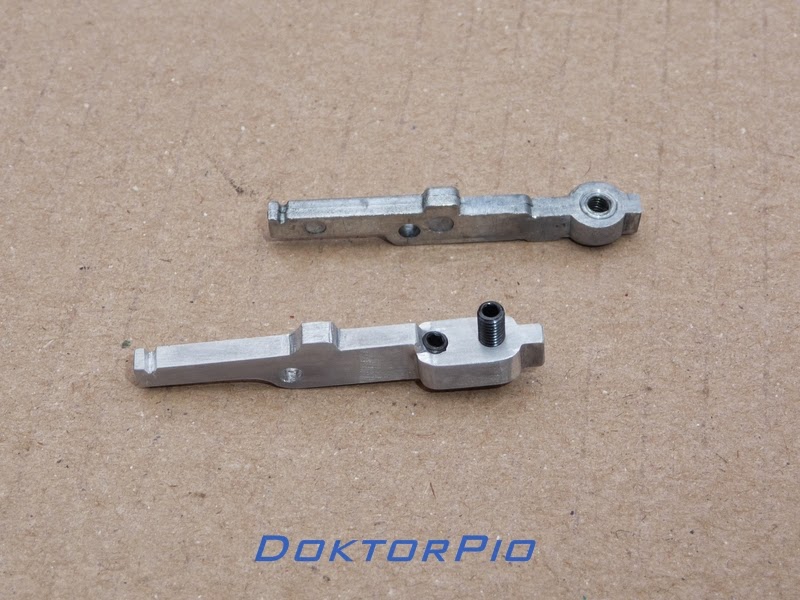
Zastosowałem podkładki kasujące luzy między poszczególnymi mechanizmami. Podczas składania spustu elementy trące delikatnie smarowałem odpowiednim rzadkim smarem. Mniejsze luzy to bardziej precyzyjne działanie. Wszystkie te poprawki wpłynęły na większa przewidywalność miękkość i precyzję spustu

1- tworzywo PET 2 -taśma teflonowa zbrojona.

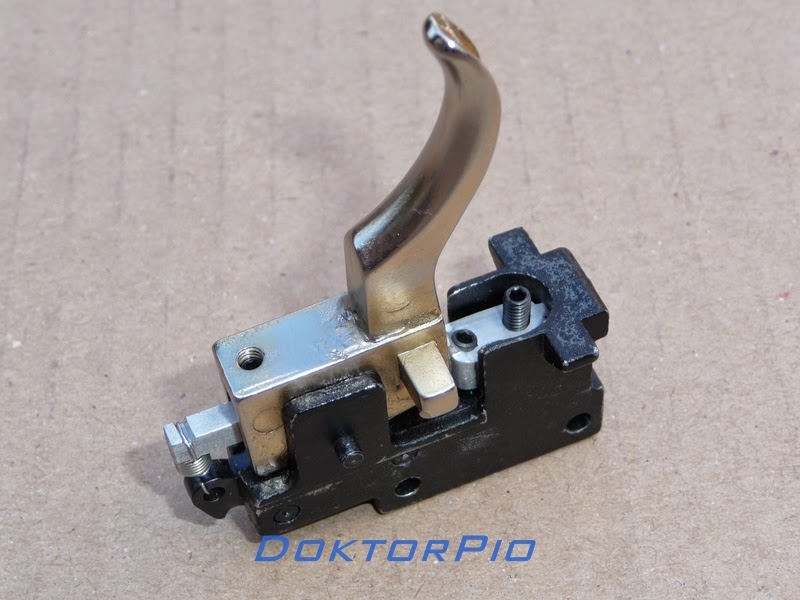
Poprawa mechanizmu indeksacji magazynka. Zastosowałem przekładki z taśmy teflonowej zbrojonej samoprzylepnej oraz z tworzywa PET.
Poniżej wszystkie elementy przed smarowaniem i złożeniem.



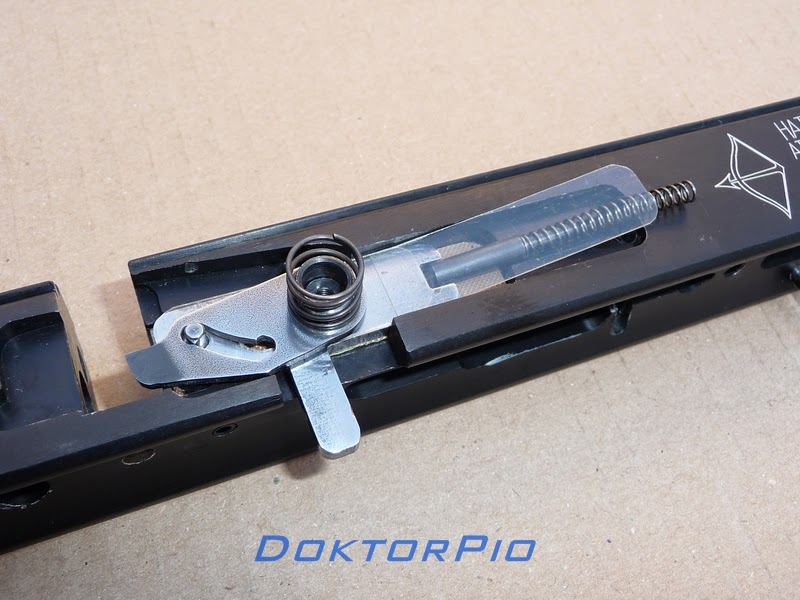
Zmodyfikowałem zapadkę popychającą magazynek. Szlifowałem detal pod odpowiednim kątem tak żeby bardziej precyzyjnie popychał magazynek.
Wszystkie te poprawki wpłynęły na poprawienie płynności i lekkości działanie mechanizmu indeksowania magazynka ! Naprawdę warto poprawić ten mechanizm, polecam :-D

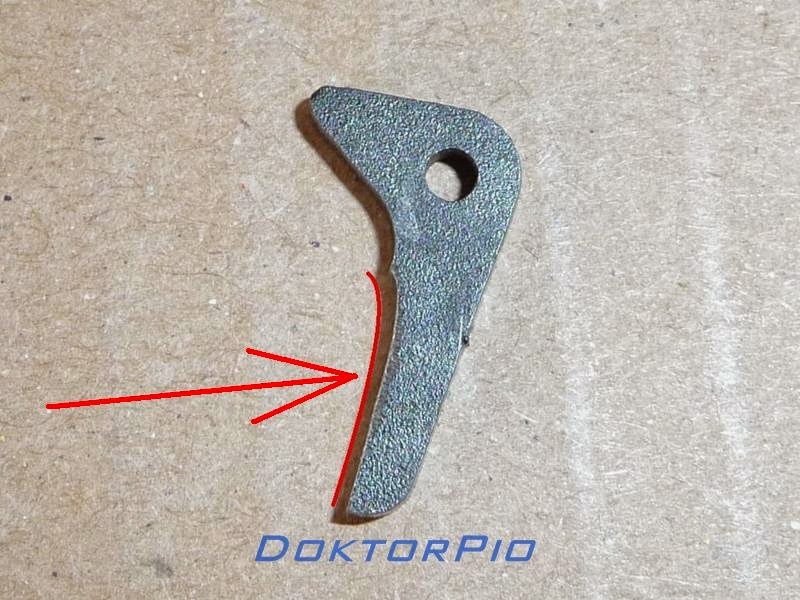

Czas na koronę lufy oraz port ładowania. Generalnie nie było źle ale poprawiłem moim ulubionym

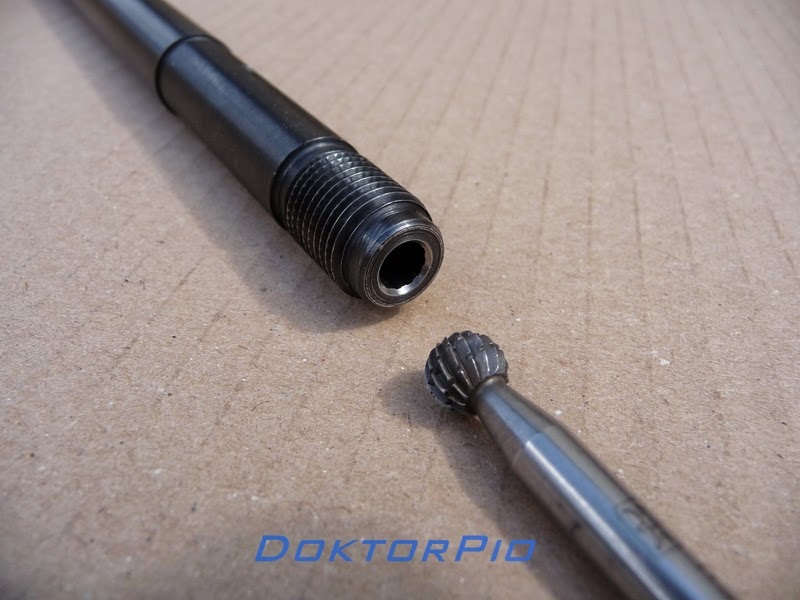

No i największy bubel w tym karabinku

Trudno było coś sensownego wymyślić hmm ... ? Wyfrezowałem otwór w lufie pod skosem względem otworu transferportu i efekt został osiągnięty


Kolejny element wymagający poprawki to popychacz śrutu. Na fotce poniżej widać miejsce gdzie są wytarte bruzdy na skutek tarcia o element blokujący zbijak, no cóż taka konstrukcja :-/ Wyszlifowałem papierem wodnym wydarte powierzchnie i wypolerowałem element blokujący i popychacz.
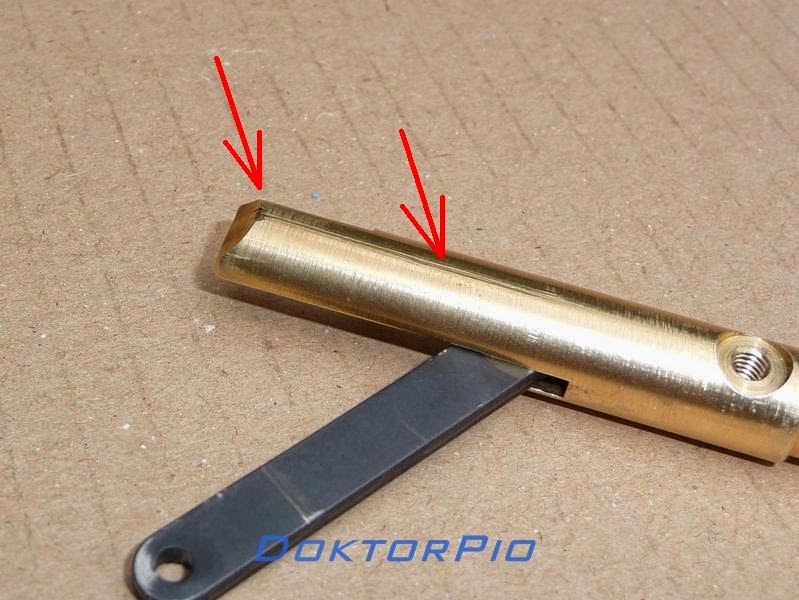
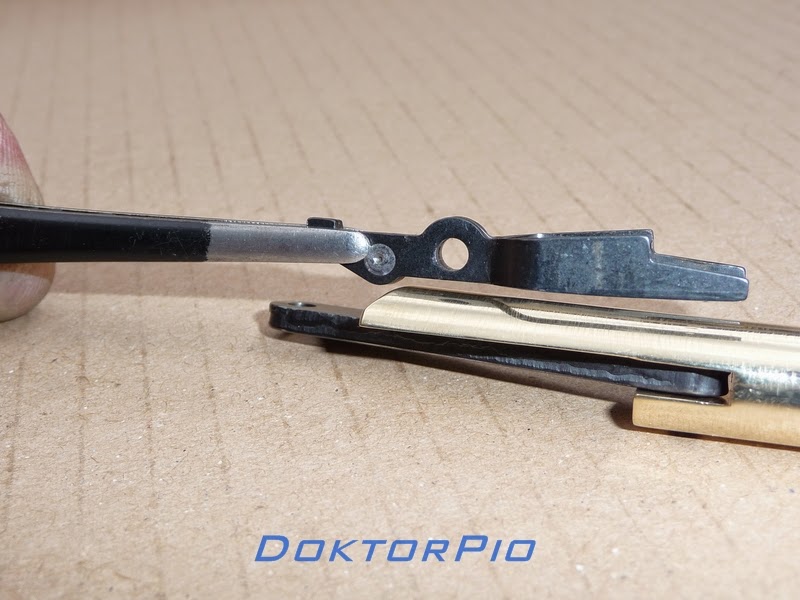
Popychacz wypolerowałem, tuleja prowadząca wykonana jest z metalu i posiada duży luz względem popychacza, co przekłada się na nieprecyzyjną pracę popychacza. Dorobiłem nową bardziej spasowaną tuleje prowadzącą z poliamidu PA6. Zyskałem bardziej precyzyjna pracę popychacza i zniknął problem z rysowaniem się popychacza :-D

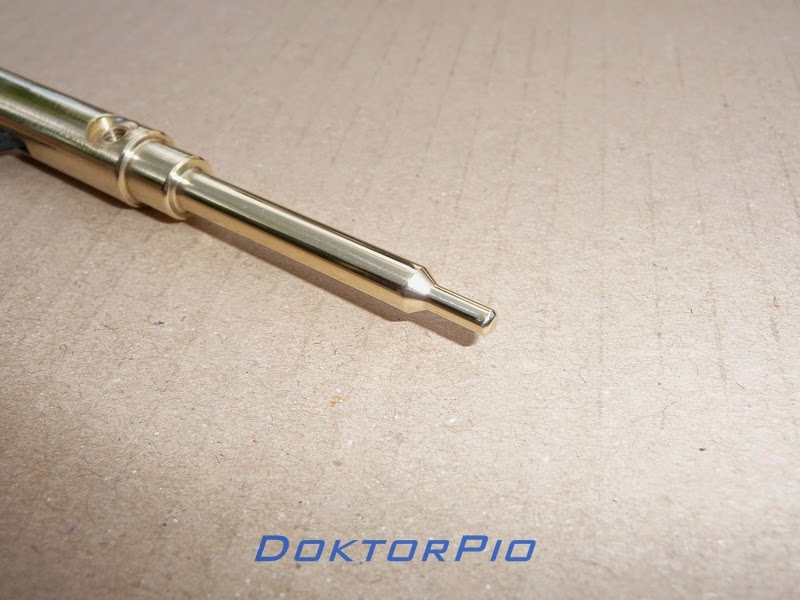

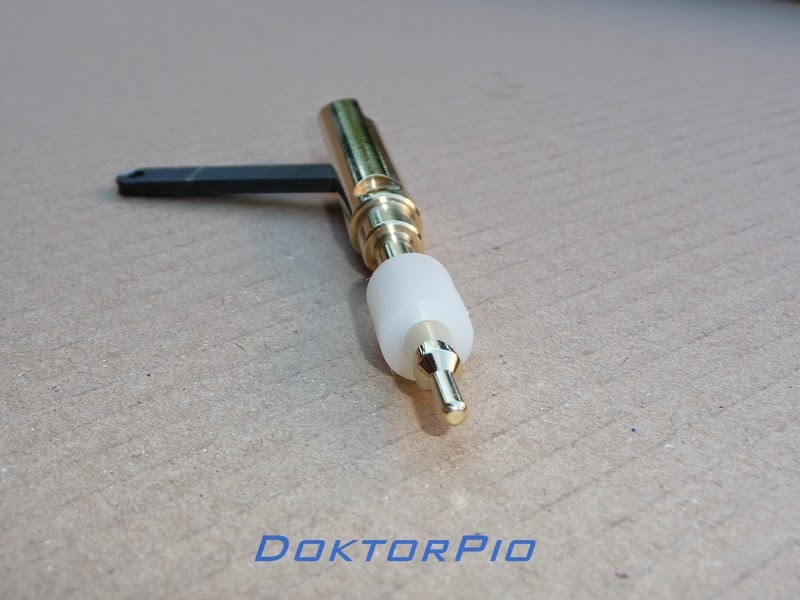
Miejsca zaznaczone zielonymi strzałkami powodują kaleczenie krawędzi zbijaka. Skaleczony zbijak rysuje powierzchnię cylindra w którym się porusza ! Zeszlifowałem te krawędzie pod odpowiednim kontem a następnie wypolerowałem.
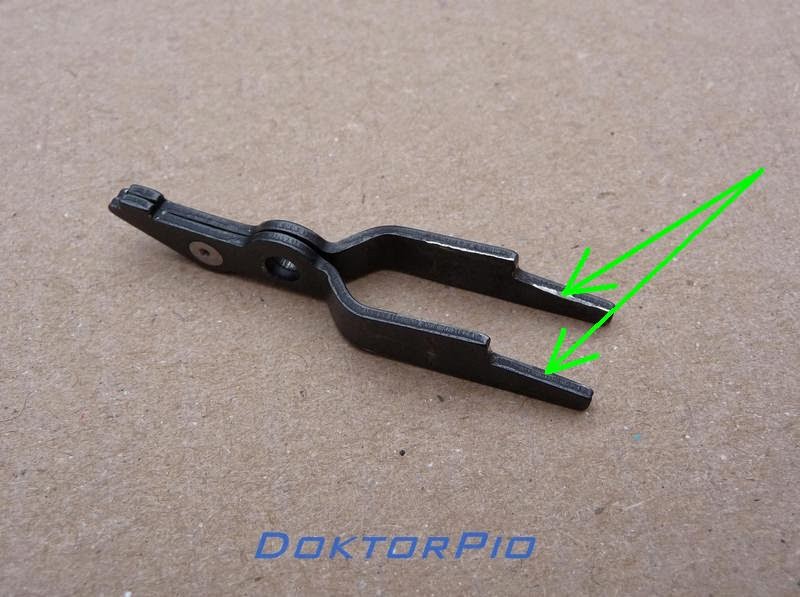
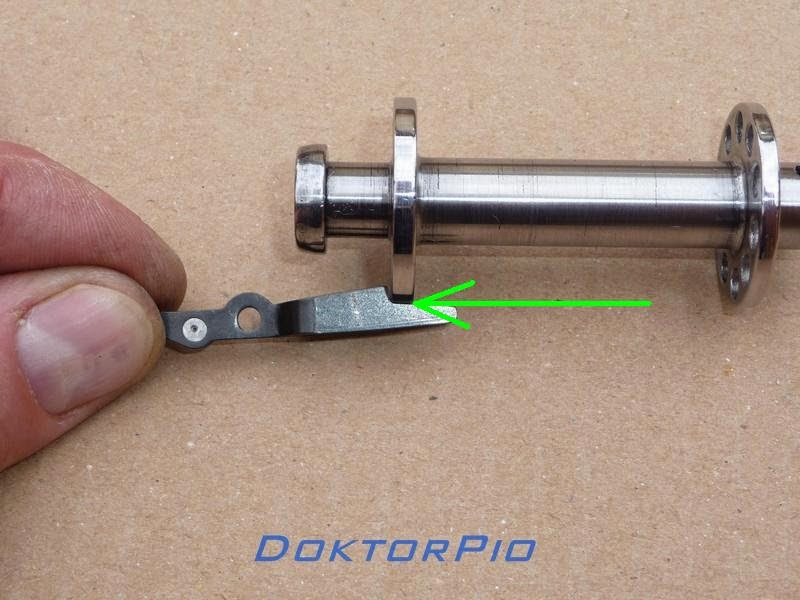
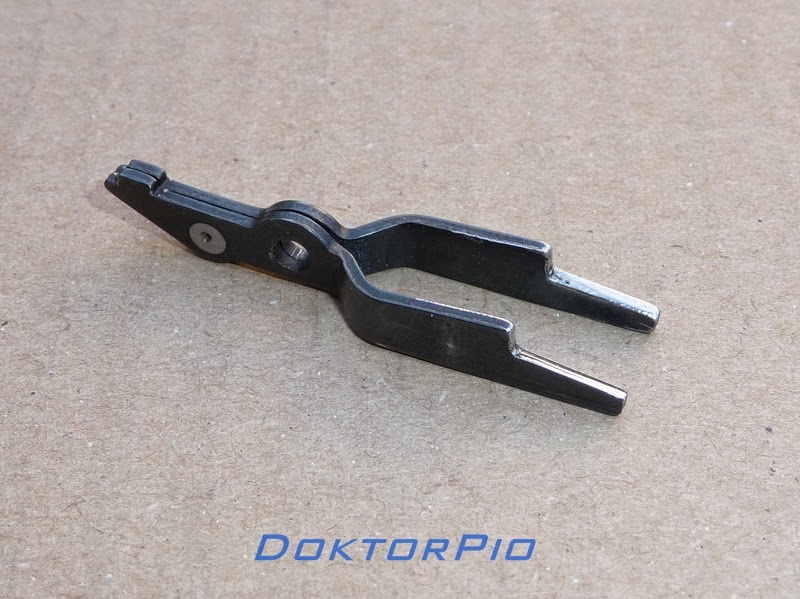
Zmniejszyłem wagę zbijaka do 40g nawiercając otwory wiertłem 4mm. Następnie wyszlifowałem i wypolerowałem zbijak. Wypolerowałem również cylinder w którym się porusza zbijak ale zapomniałem zrobić fotek ;laughing:
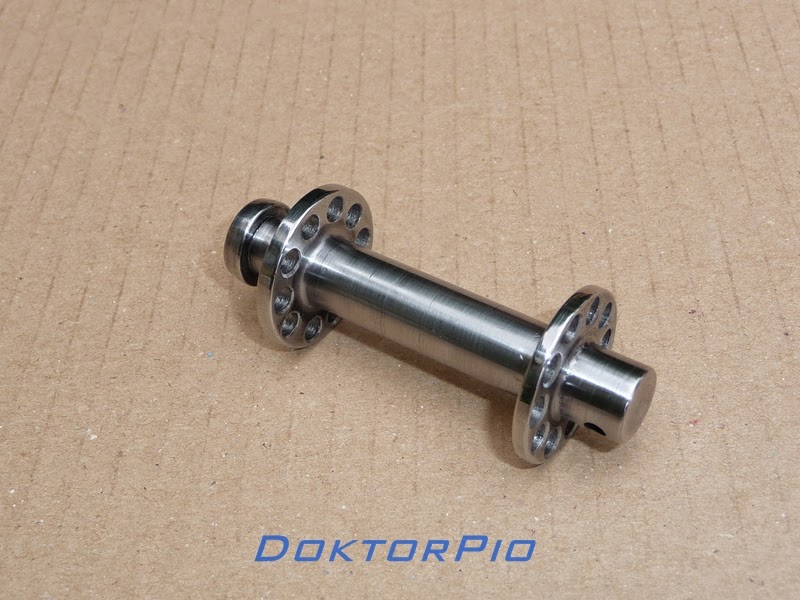
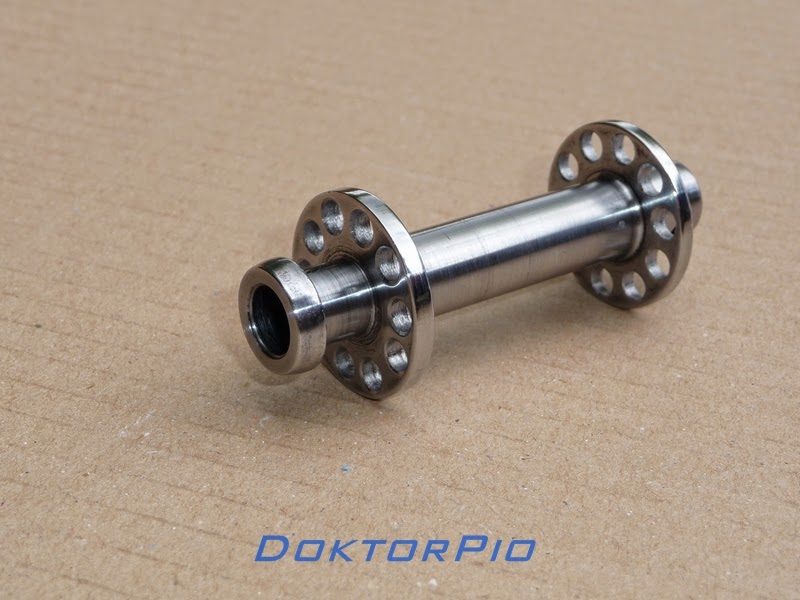
Końce sprężyny zbijaka są nieobrobione postanowiłem je wyszlifować i wypolerować. To pozwoli na swobodne skręcanie się sprężyny wokół własnej osi podczas napinania i luzowania sprężyny w czasie jej pracy. A to przełoży się na powtarzalność pracy zbijaka !
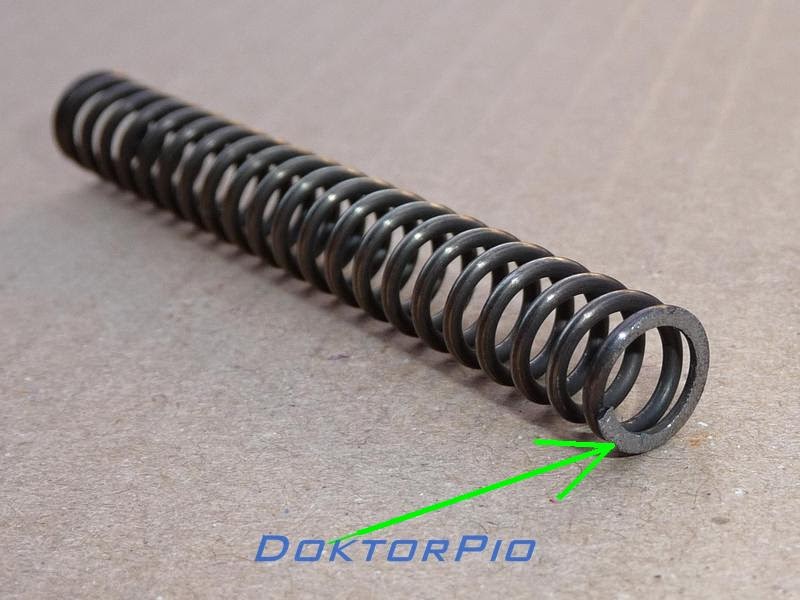
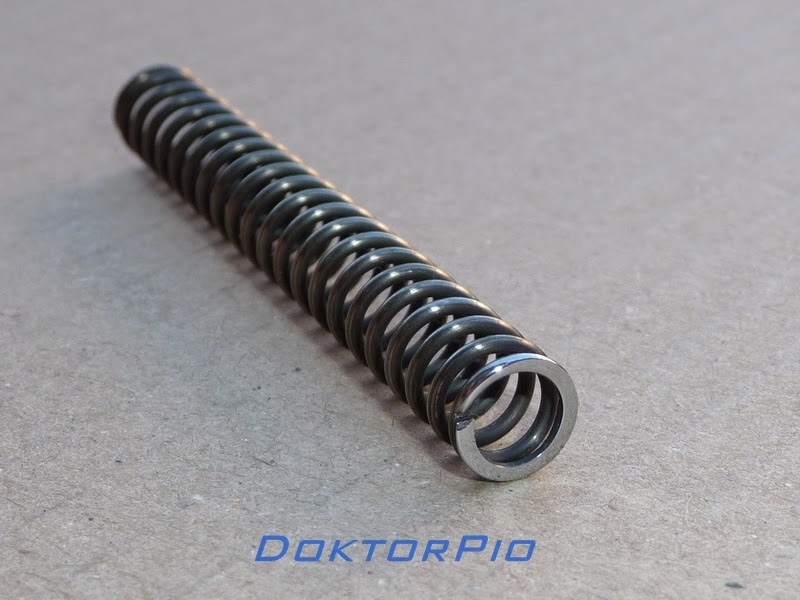
Kolejny Turecki bubel to zastosowanie śrubki która ma ograniczać ruch zbijaka, wówczas kiedy mamy wykręcony kartusz. Jeśli wykręcimy kartusz i przeładujemy karabinek a następnie strzelimy, to spowoduje że zbijak zatrzyma się na gwincie śrubki którą widzimy poniżej a nie na iglicy zaworu kartusza. Kilkukrotne takie strzelenie bez kartusza spowoduje uszkodzenie śrubki jak poniżej i kaleczenie się zbijaka

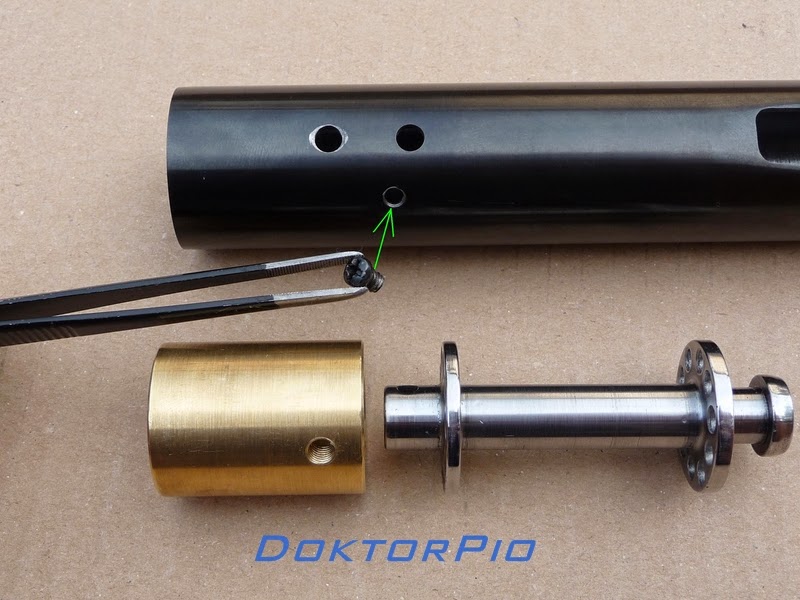

Śrubkę wyrzuciłem i zastosowałem gumowy odbój przyklejony taśmą dwustronna do mosiężnego elementu. Takie rozwiązanie znacznie lepiej spełni swoje zadanie. Oczywiście należy dobrać odpowiednią grubość odbojnika, ażeby nie ograniczyć zakresu pracy zbijaka podczas normalnej pracy tj z wkręconym kartuszem !
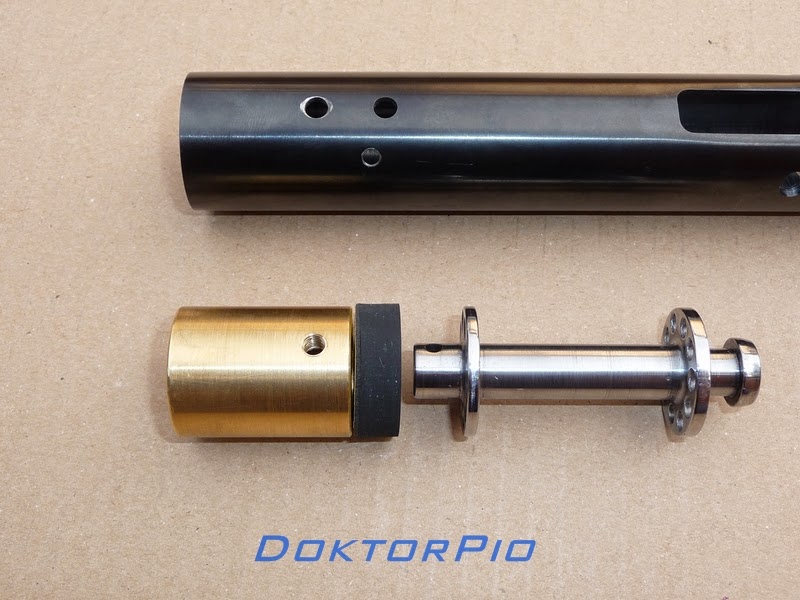
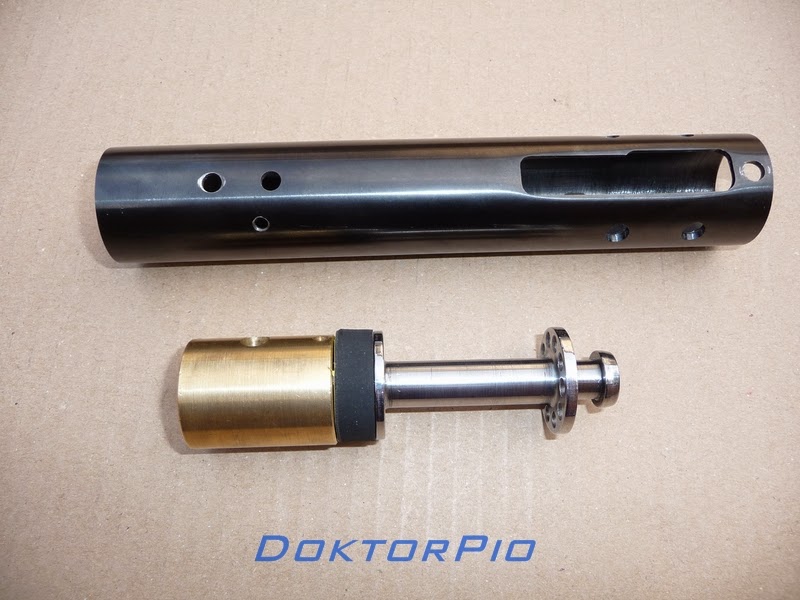
Zaczynam składać poszczególne elementy karabinka elementy metalowe które pracują popychacz śrutu, zbijak smaruję cieniutko specjalnym rzadkim smarem i olejem. Elementy takie jak oringi smaruje smarem silikonowym.
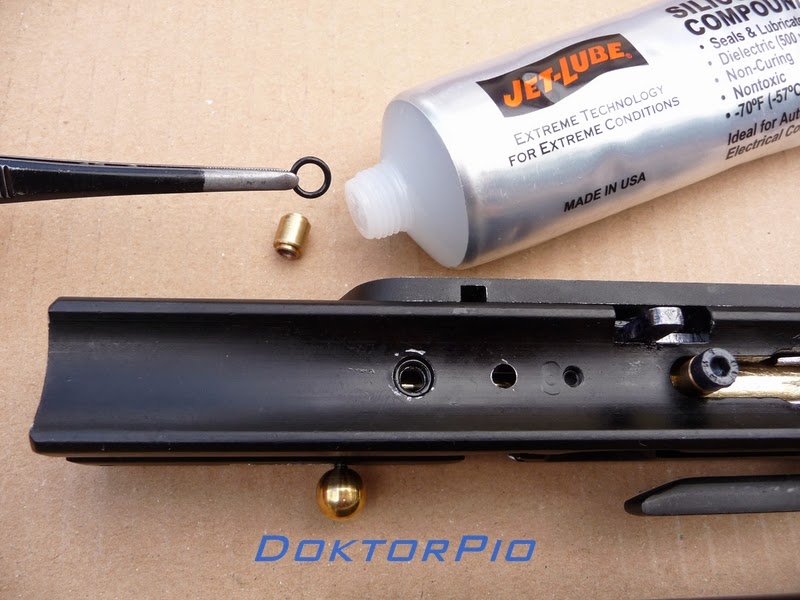
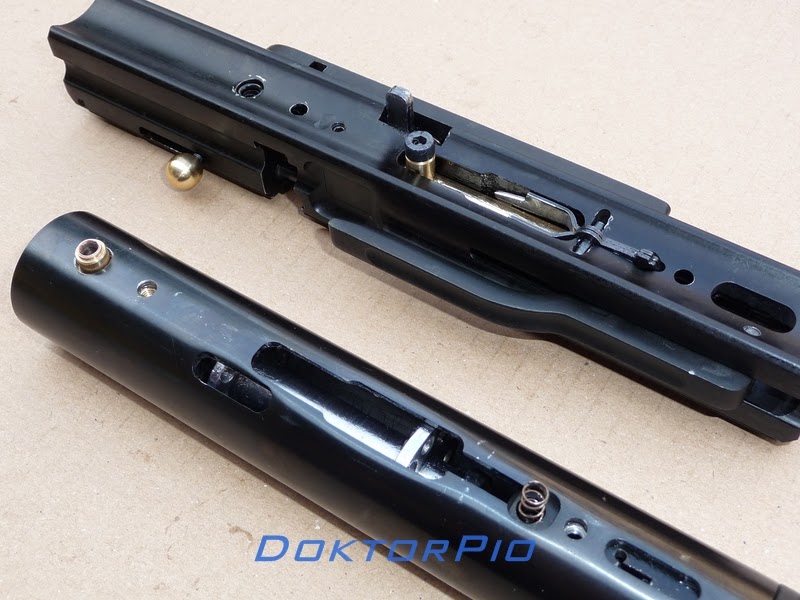
Czas zabrać się za kartusz. Kartusz został rozkręcony na drobne części i umyty, osuszony i tylko nasmarowany odpowiednimi olejami.
Zamontowałem regulator Andriusa wcześniej oczywiście wiercąc w kartuszu wymagany otwór potrzebny do prawidłowej pracy regulatora.
Dla dociekliwych wszystkie testy i pomiary były wykonane poza granicami RP gdzie nie obowiązuje limit 17J !
Typowy krótki kartusz ma pojemność 180cm3 po zastosowaniu regulatora oraz komory strzałowej o objętości 12cm3 pojemność kartusza zmniejszyła się do 150cm3.
Ciśnienie na jakie jest ustawione regulator to 125bar
Sprężynka zbijaka limitowa ustawiona na maksymalne napięcie co dawało około 38J
Wyniki były następujące.
Pojemność kartusza 150 cm3
Kartusz naładowany do 200bar
Oddane 24 stabilne strzały (38J) do osiągnięcia 125bar
Rożnica w ciśnieniu 75 bar
Liczymy

150cmx75bar=11250ml powietrza
11250ml /24strzały= 468ml powietrza na 1 strzał
75bar /24strzałów = 3.125 bara na 1 strzał -ten wynik o niczym tak naprawdę nam nie mówi co opiszę poniżej w tym temacie !
Wynik 24 stabilnych strzałów jak dla mnie nie były zachwycający :-/
Tak wiec przystąpiłem do modyfikacji i i ulepszenia zaworu kartusza celem zwiększenia ilości oddawanych strzałów.
Wypolerowałem otwór w który wchodzi iglica na którą jest założony malutki oring. Według mnie jest to dość istotne miejsce, mające wpływ na powtarzalność pracy iglicy a to jak wiadomo na powtarzalność strzałów o takiej samej energii.
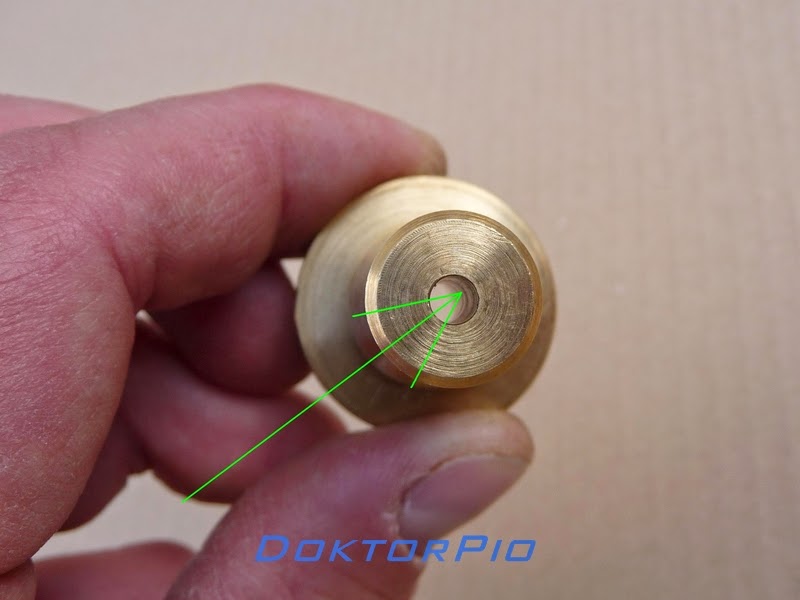
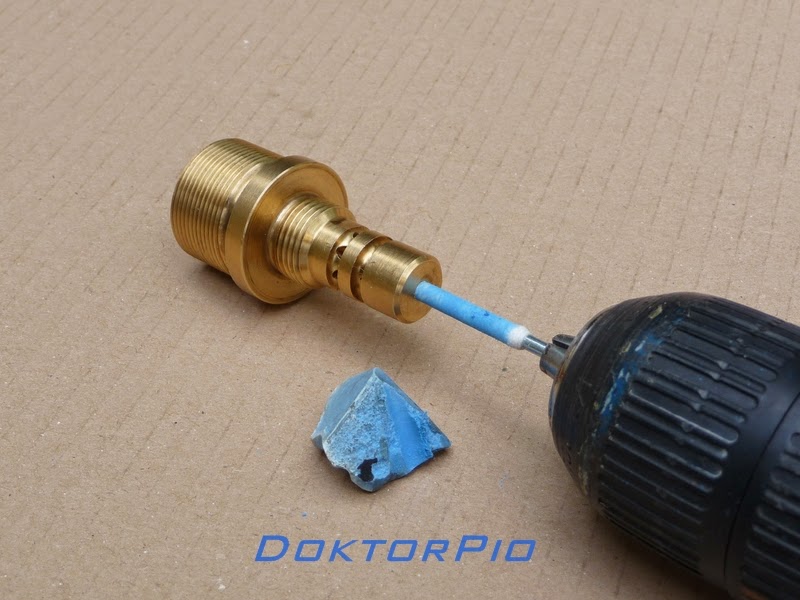
Iglica tez została wypolerowana :-D

Kolejna zmiana to wykonanie w zaworze kartusza centralnego otworu dolotowego do transferportu, zamiast kilku małych otworków i przetoczenia. Ma on znaczenie na ilość zużywanego powietrza podczas oddania strzału.
Są rożne metody zrobienia tego patentu co niektórzy toczą cały nowy element i wiercą w odpowiednim miejscu otwór. Inni zalutowują twardym lub miękkim lutowiem otworki.
Ja osobiście zastosowałem najprostszą metodę zaklejenia otworów specjalnym dwuskładnikowym klejem firmy Chester Molecular. Jest to profesjonalny klej stosowany do naprawy i regeneracji wałów, zębatek, łopatek wirników i korpusów pomp.
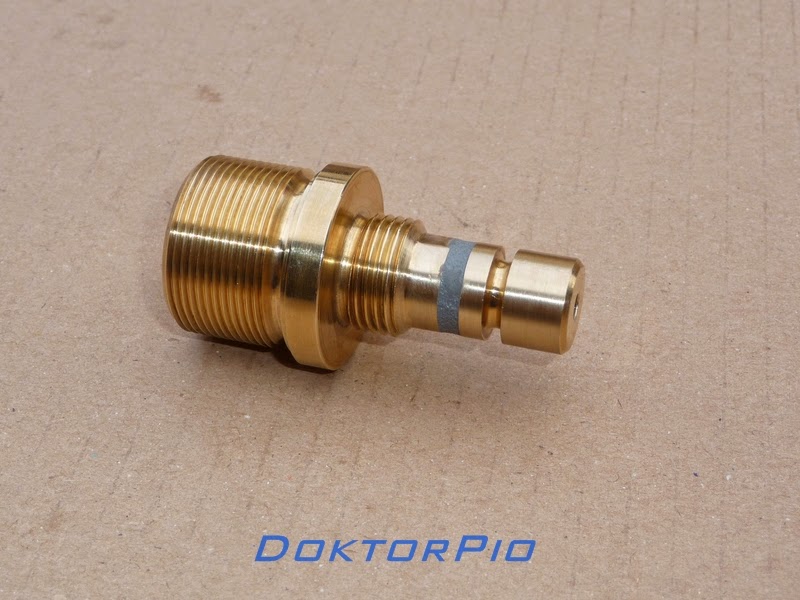
Po stwardnieniu kleju wkręciłem króciec w gniazdo a następnie zaznaczyłem miejsce gdzie ma być umiejscowiony centralny otwór.
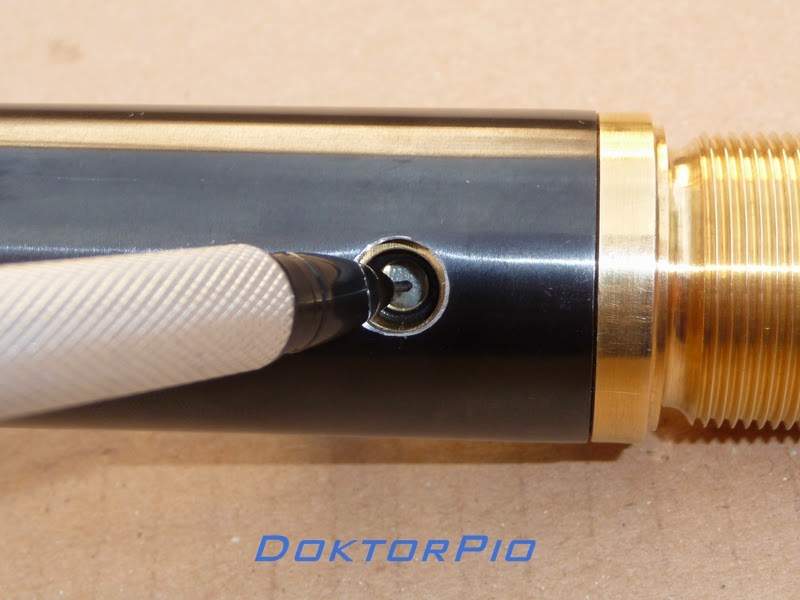
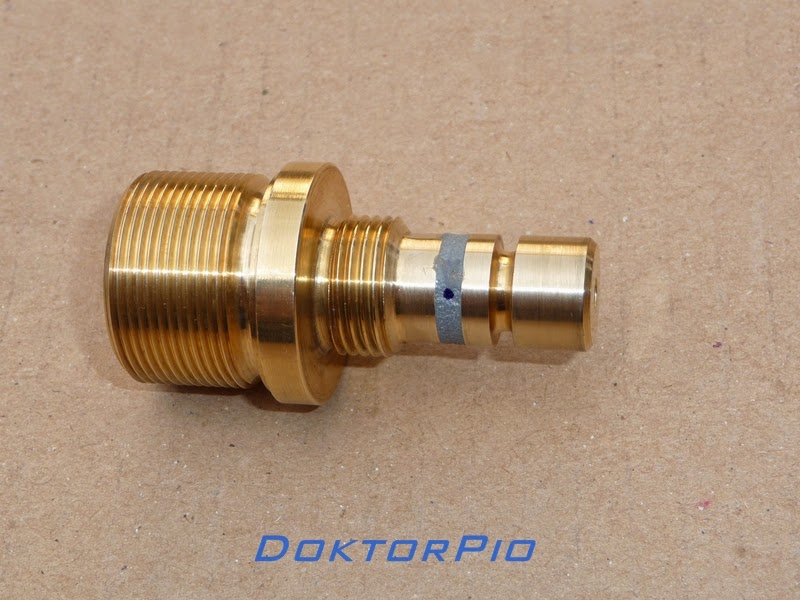
Następnie wywierciłem otwór wiertłem 3.5mm. Polecam wiercić otwór po zamontowaniu wierconego elementu w uchwycie (imadle) celem uniknięcia "ściągnięcia" na bok podczas wiercenia otworu !


Po złożeniu zaworu do kupy wygląda to tak
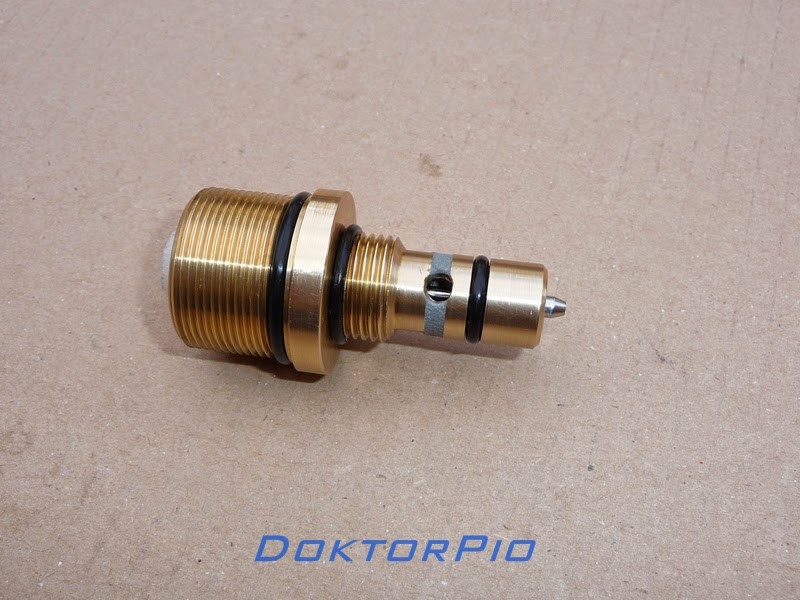
Tak jak pisałem wcześniej zamontowałem regulator Andriusa .
Typowy krótki kartusz ma pojemność 180cm3 po zastosowaniu regulatora i komory strzałowej o objętości 12cm3 pojemność kartusza zmniejszyła się do 150cm3.
Pierwszy pozytywny efekt jaki zaobserwowałem po modyfikacjach to wzrost energii przy tym samym ustawieniu sprężynki zbijaka !
Wniosek jest taki że zmniejszenie zbędnych pustych przestrzeni na zaworze kartusza spowodowało że ta sama ilość powietrza wypuszczona przez zawór podczas strzału idzie w lufę a tym samym mamy większą energię.
Ciśnienie na jakie jest ustawione regulator to tak jak poprzednio 125bar co daje po modyfikacjach energię na poziomie 40,6-41,0J. Ustawiłem więc sprężynkę zbijaka tak jak przed modyfikacją na energię 38J.
Test wykonany na śrucie exact heavy.
Temperatura zew. podobna jak przy poprzednim teście przed modyfikacjami kartusza.
Po zrobionych czarach marach na karabinku wyszły następujące wyniki.
Pojemność kartusz 150 cm3
Kartusz naładowany do 200bar
Oddanych 30 stabilnych strzałów do osiągnięcia 125bar
Rożnica w ciśnieniu 75 bar
Liczymy

150cmx75bar=11250ml powietrza
11250ml /30strzałów= 375ml powietrza na 1 strzał
75bar /30strzałów = 2.5 bara na 1 strzał
Tak więc jak widać poczynione zabiegi przyniosły pozytywny skutek w postaci mniejszego zużycia powietrza na 1 strzał co przekłada się na liczbę oddanych strzałów z jednego ładowania kartusza.
Jeśli chodzi o pewną wartość pomiaru jaką często podają koledzy i ja sam przytoczyłem chodzi mi o ciśnienie w barach na 1 strzał jest to wartość którą możemy wykorzystywać tylko i wyłącznie w przypadku kartuszy o tej samej pojemności !
Ta wartość jest zmienna w zależności od wielkości kartusza im większy kartusz tym spadek ciśnienia na 1 strzał jest mniejszy

Podam przykład na podstawie drugiego pomiaru dla kartusza o pojemności nie 150cm3 a 300cm3
Czyli nie będziemy mieli 30 oddanych strzałów a 60
Zużycie powietrza z 200bar do 125bar =75bar
300cmx75bar=22500ml zużytego powietrza
22500ml /60strzałów= 375ml powietrza na 1 strzał
75bar /60strzałów = 1.25bara na 1 strzał ???
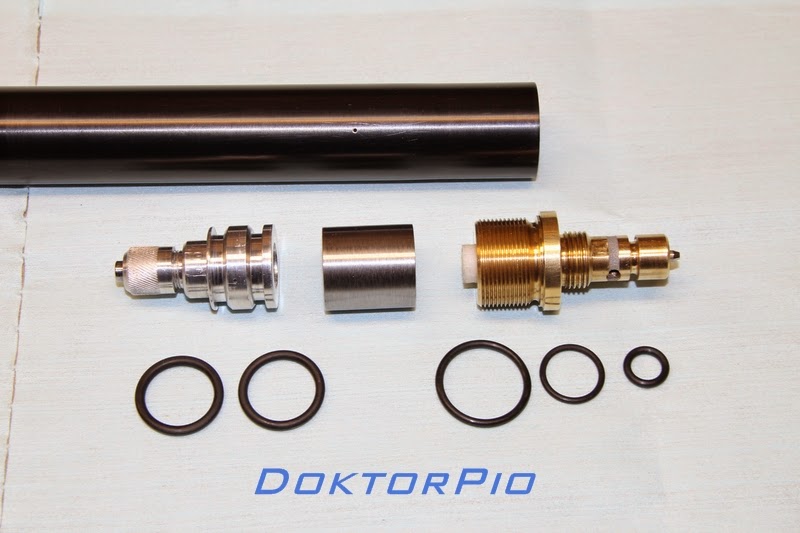
W wolnej chwili zrobię pomiary ilości oddanych strzałów z jednego ładowania kartusza dla wersji w limicie.
Etap I moich modyfikacji został zakończony karabinek został złożony efekty na tarczy strzeleckiej są bardzo zadowalające. Ale tak naprawdę karabinek ma być przerobiony na wersję BULLPUP. Więc zabieram się do drugiego etapu modyfikacji

Etap II
Etap II tak jak pisałem obejmie zaprojektowanie mechanizmów oraz osady do systemu BULLPUP. Wykonanie wszelkich prowadnic cięgien i innych elementów. Wykonanie osady BULLPUP. Anodowanie elementów aluminiowych. Wykończenie osady olejami itp.
Po wszelkich pomiarach karabinka i wyliczeniach zaprojektowałem wstępnie na kartce cały system bullpup. Następnie wszystkie zaprojektowane elementy narysowałem w programie AutoCad po czym eksportowałem projekty do programu LazyCam który przełożył je na tryb maszynowy zrozumiały dla maszyny CNC. Oczywiście musiałem wpisać rodzaj narzędzi ilość cykli przejazdów narzędzia, głębokości szybkości posuwu itp. Tak przetworzone projekty lądują w programie WinPC-NC który obsługuje frezarkę CNC.
Miałem jeden problem związany z długością pola pracy frezarki było ono mniejsze od długości prowadnicy i dolnej szyny :-/ Ale i z tym dałem sobie rade :-D
Kolejną istotną sprawa było gwintowanie otworów od elementów cięgien i prowadnic. Chodzi o to że gwintowanie wszystkimi trzema stopniami gwintowników (FANAR) w aluminium powodowało że gwinty były ciut luźne ! W związku z tym gwintowanie kończyłem na 2 stopniu, co powodowało że gwinty w otworach nie były zbyt luźne
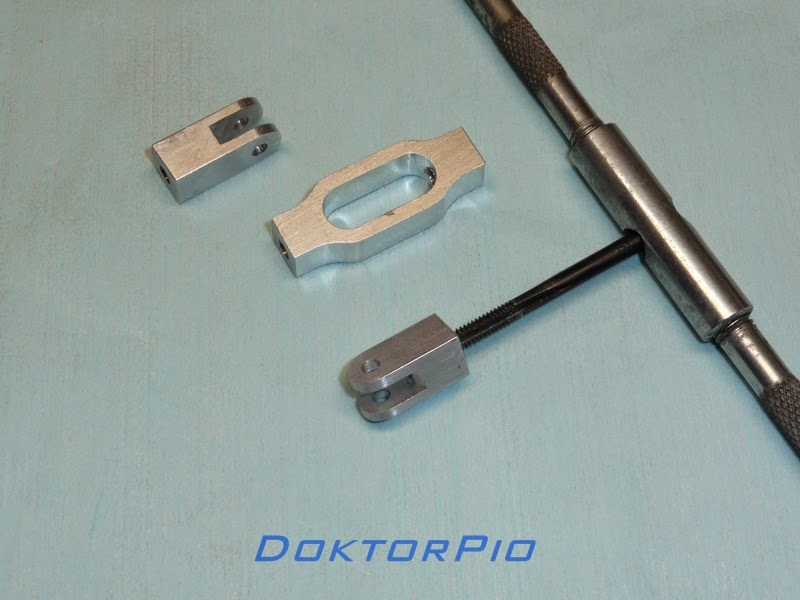
Wykonałem dodatkowy element spustu do systemu bullpup, to ten detal u góry ten element niżej zrobiłem wcześniej. Boki jednego z elementów okleiłem zbrojoną taśma teflonową celem zmniejszenia oporów tarcia miedzy tymi dwoma elementami :-D
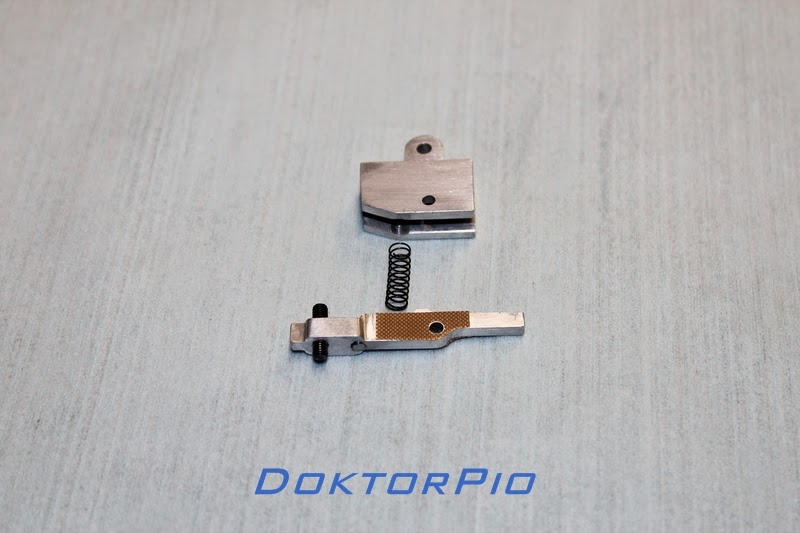

Za pomocą imbusowych śrub regulacyjnych spust obecnie ma szeroki zakres regulacji pracy poszczególnych stopni pracy a także położenia spustu. Co pozwala na wyregulowanie spustu pod swoje upodobania.

Kolejne elementy spustu, cyngiel ,cięgna, łączniki, sworznie, śruby, przekładki, sprężyny.
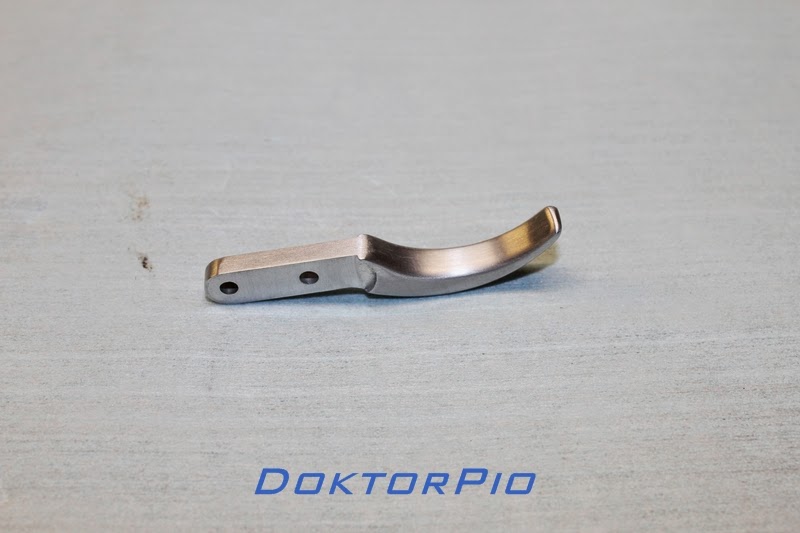
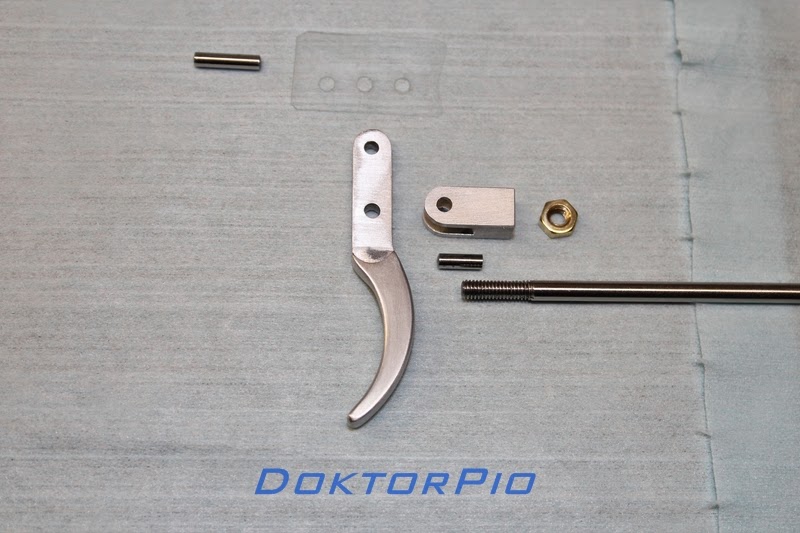
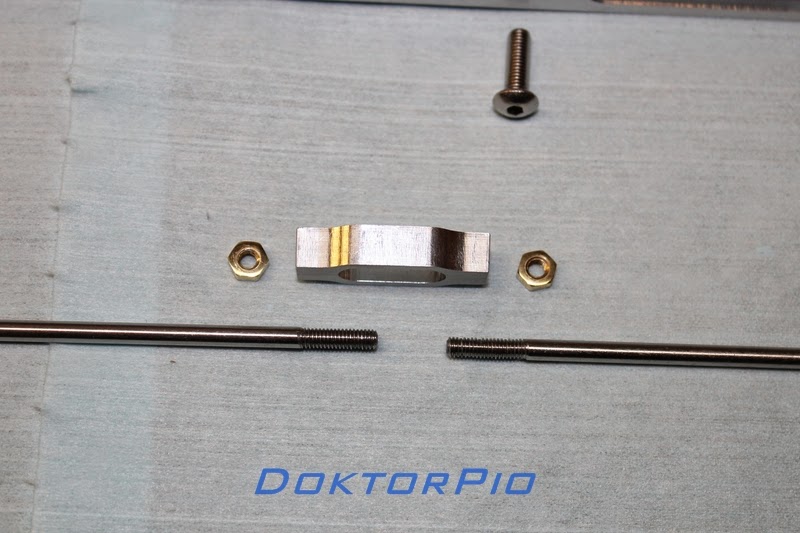

Następny element to szyna górna jest dość długa i mimo to że jest wykonana z aluminium swoje waży. Postanowiłem ją maksymalnie odchudzić wykonując frezowania mające zmniejszyć jej wagę. Frezowania górne i boczne są raczej ozdobne najwięcej materiał usunąłem od spodu prowadnicy.
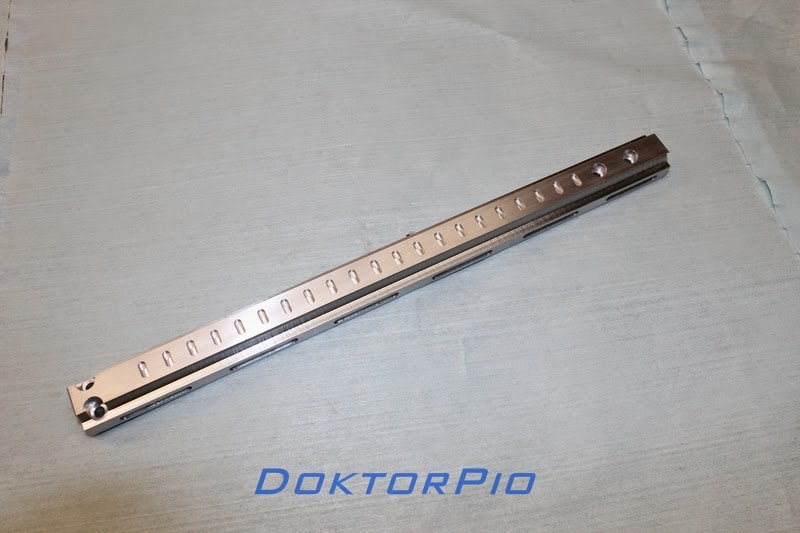
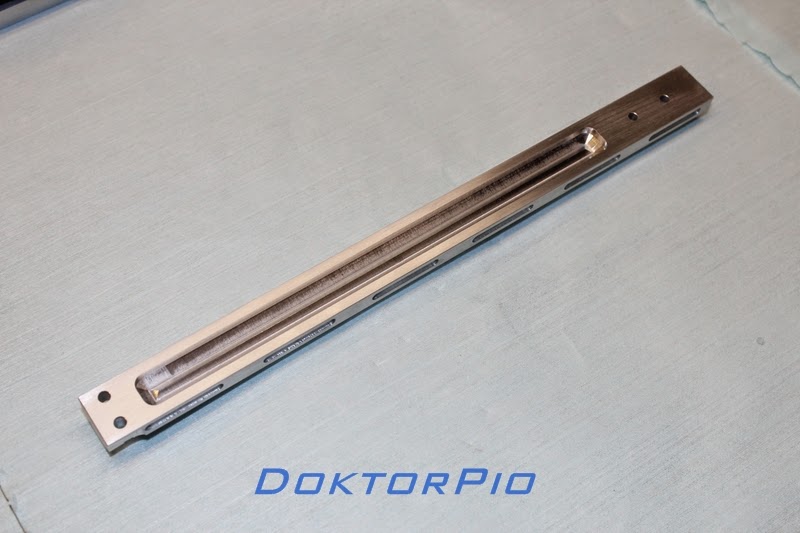
W ósemce wyfrezowałem wewnętrzne rowki pod oringi dystansujące elementy lufy i kartusza od wewnętrznych ścianek ósemki. Gdyby nie było by tych oringów to podczas wkładania kartusza następowało by rysowanie się wzajemne tych elementów.
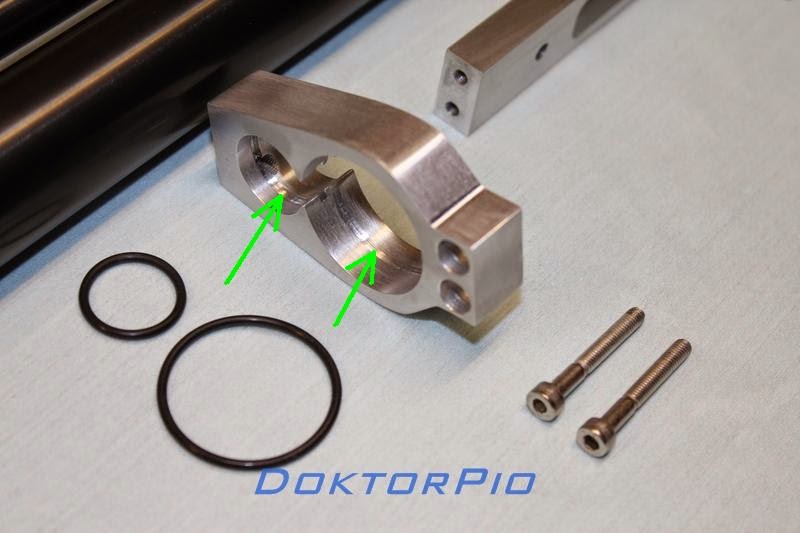

Prowadnicę dolną jak i górną odchudzałem celem zmniejszenia jej wagi.


Wyfrezowane trzy otwory widoczne na foto są przeznaczone do zamontowania cyngla spustu. Wyfrezowałem aż trzy z myślą ewentualnego swobodnego przesuwania cyngla w przód lub w tył w razie potrzeby oczywiście
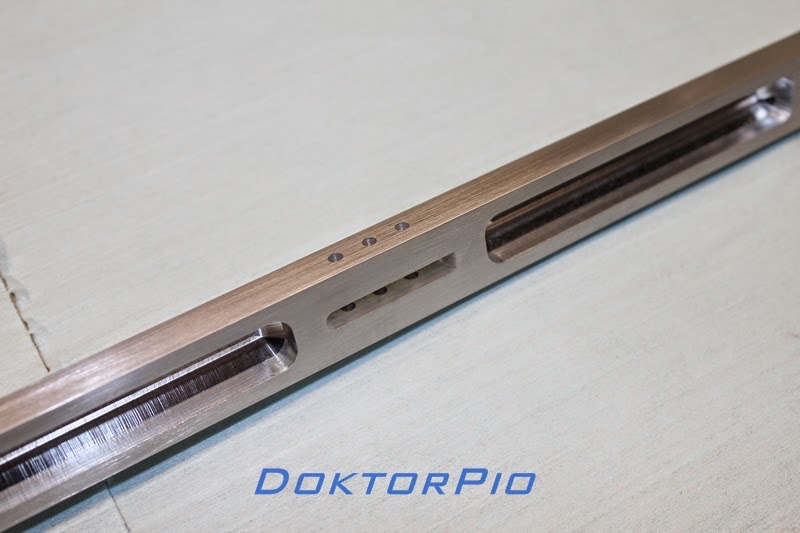
Kolejne elementy układanki zostają próbnie skręcane, prowadnica osłona lufy separator.
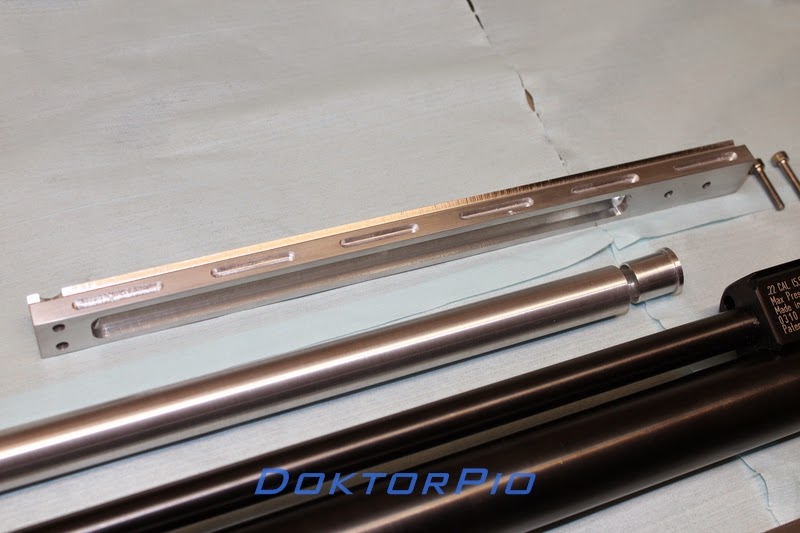


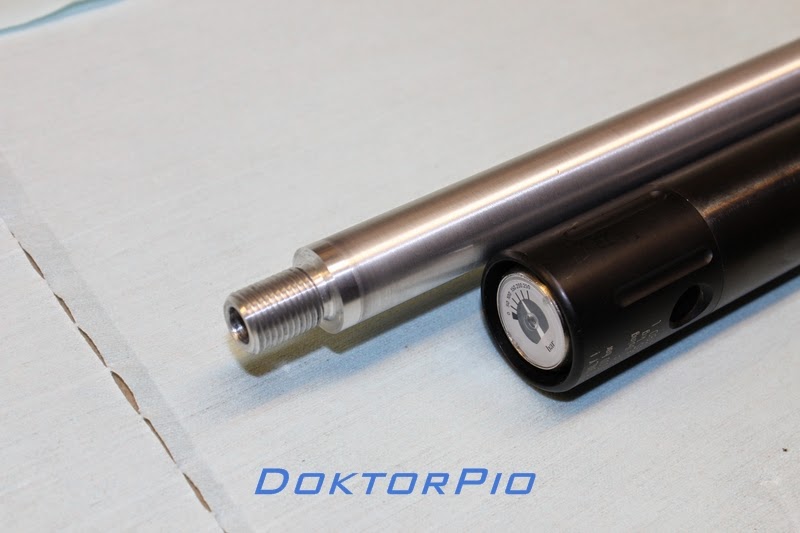
A tak się prezentują wszystkie elementy systemu bullpup przed ostatecznym wykończeniem elementów aluminiowych i przesłaniem ich do anodowania

Bink separator jeszcze nie miał frezowań
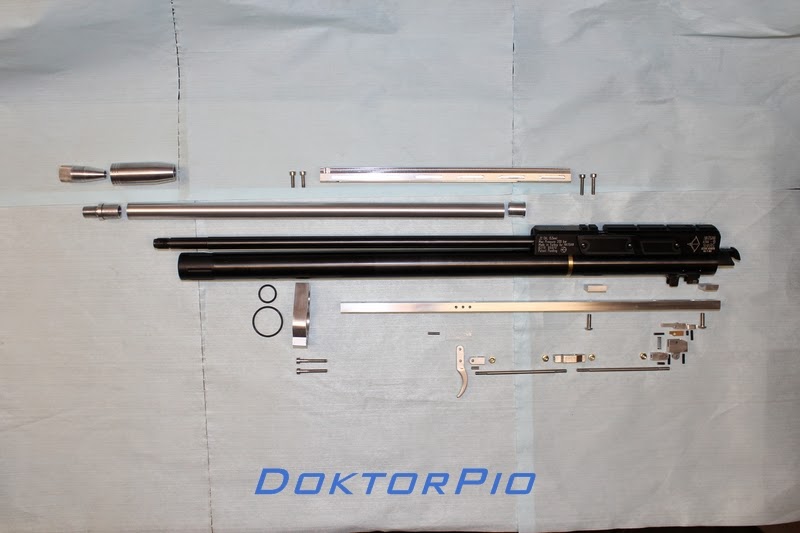
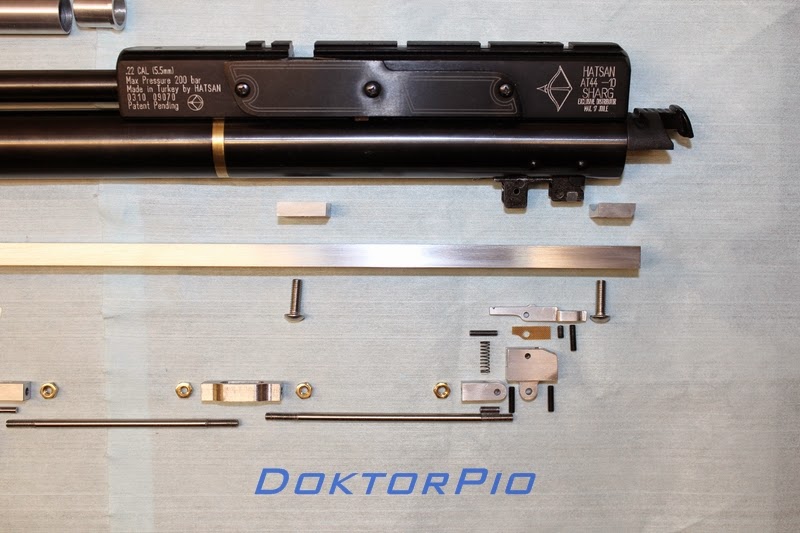
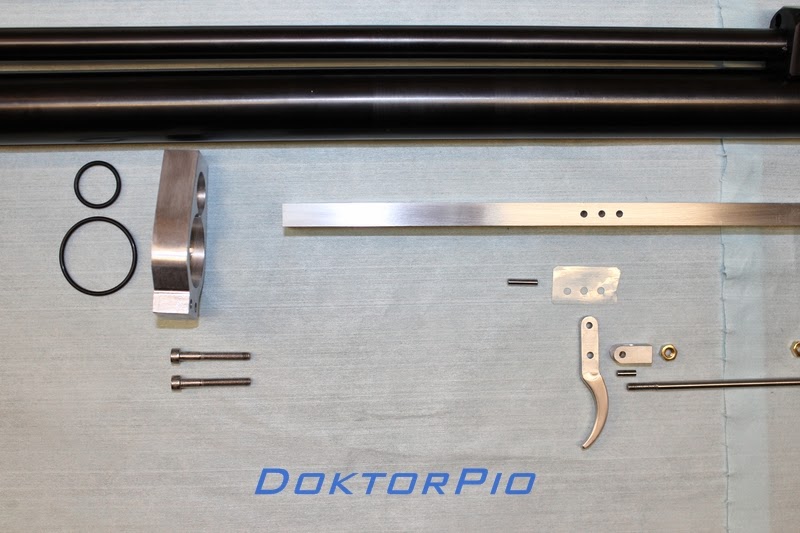
Dolna prowadnica jest w swoim przekroju prostokątem i żeby ja stabilnie przykręcić do okrągłego systemu zastosowałem specjalnie wyfrezowane podkładki aluminiowe.
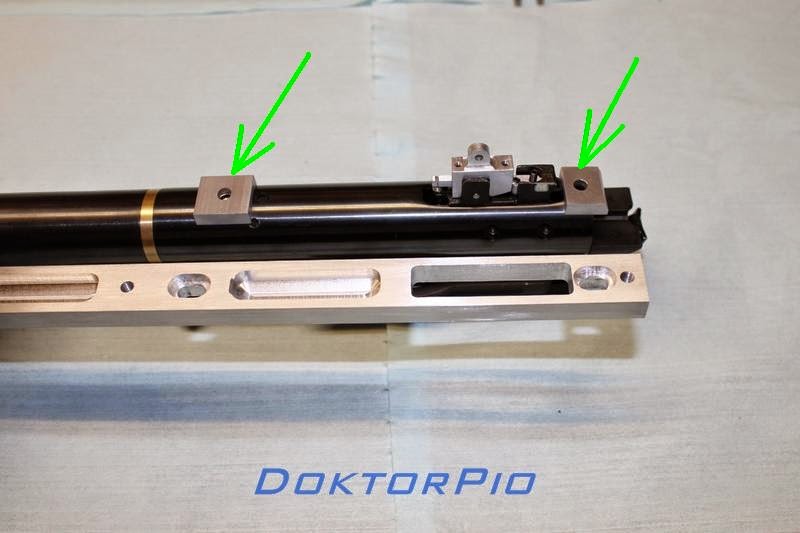

Przykręcanie ósemki do prowadnicy i górnej szyny do istniejących otworów gdzie jest blokowana lufa w bloku systemu.
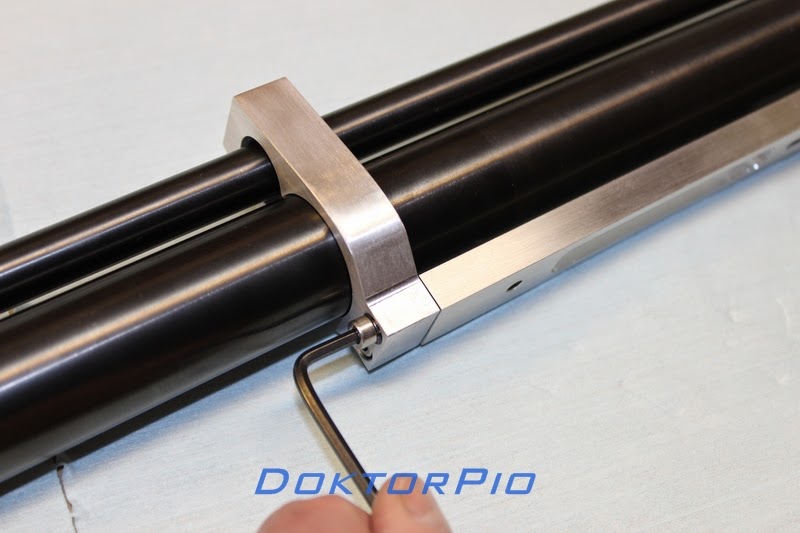
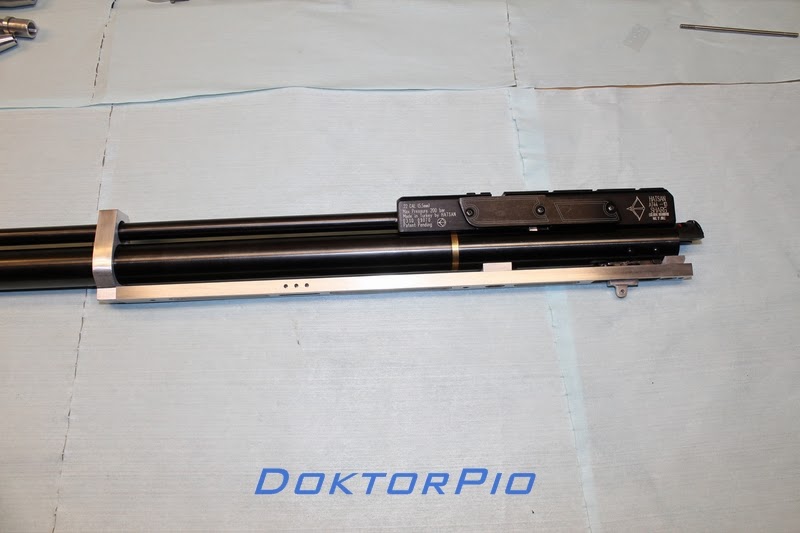
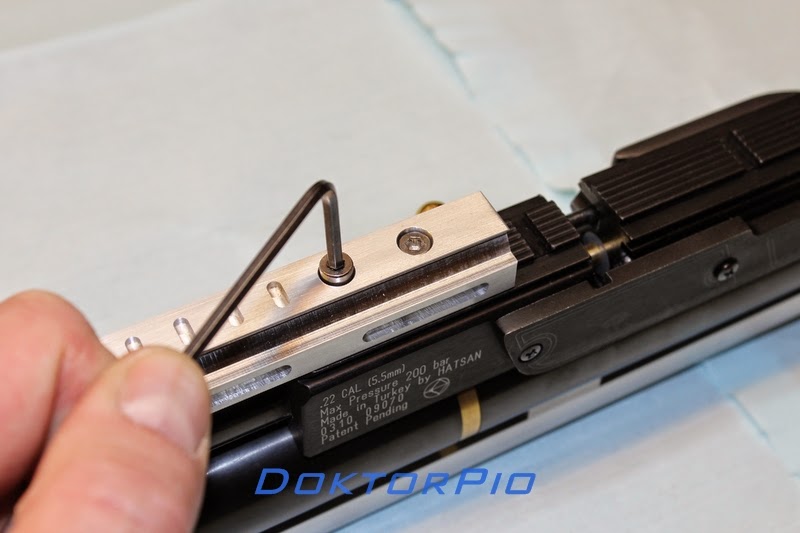
Cyngiel jest montowany w gnieździe, zastosowałem przekładki z PET celem zmniejszenia tarcia miedzy aluminiowymi elementami. Powierzchnie styku ostatecznie podczas montażu oczywiście posmarowałem delikatnie odpowiednim smarem.
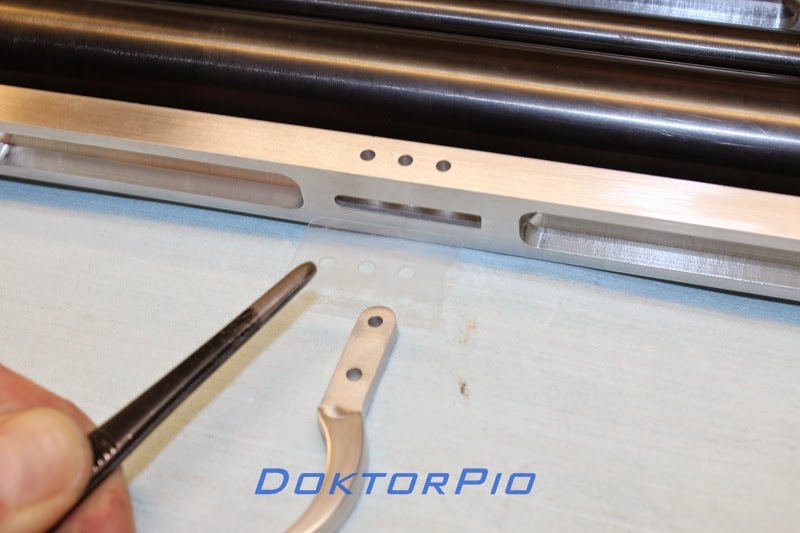
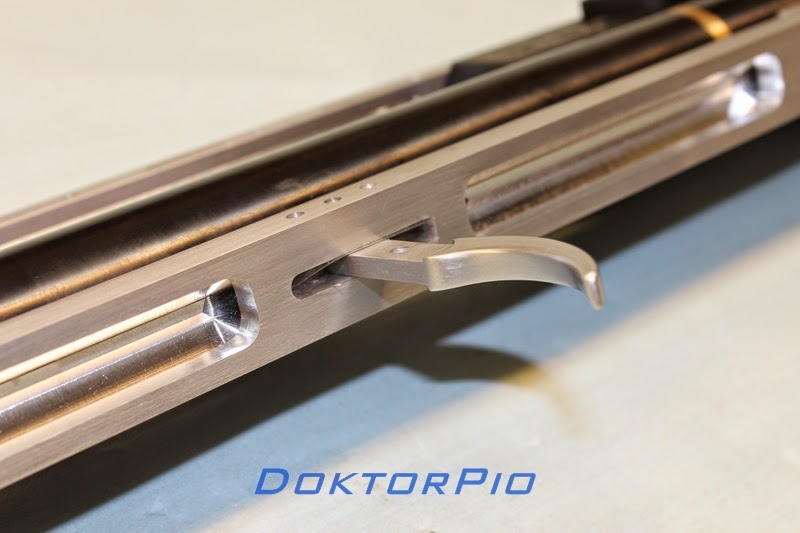
Składam poszczególne elementy całego spustu, reguluje długość cięgna kontruję wszystko nakrętkami. Sworznie i inne elementy trące smaruje delikatnie odpowiednim smarem.


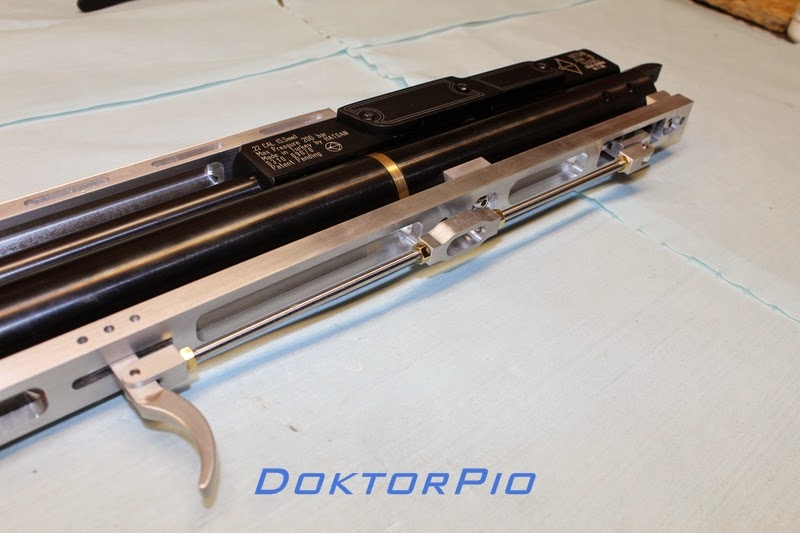
Zakładam osłonę lufy sprawdzam spasowanie wszystkich elementów.

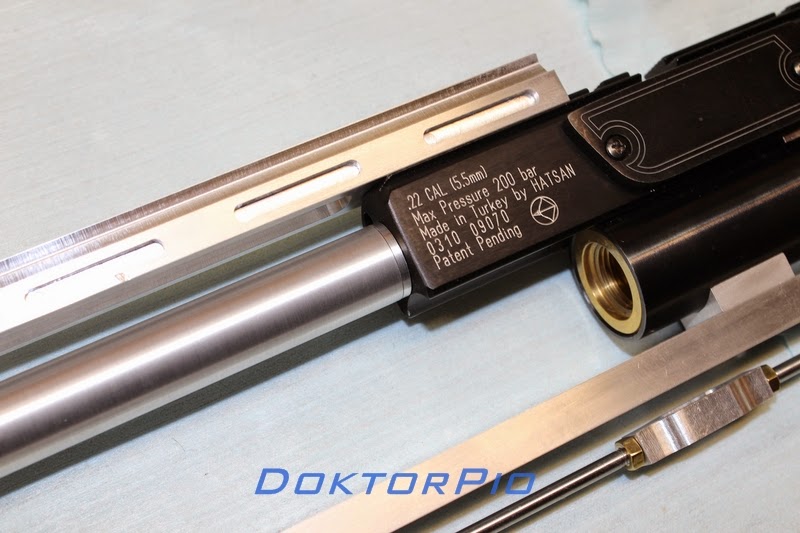
Całość systemu po skręceniu, opcja z separatorem (brak jeszcze frezowań) oraz wersja z tłumikiem od HW100



Na koniec jeszcze wymiana śrubek które skręcają system indeksowania magazynka. Zastosowałem porządne śrubki imbusowe wyglądają o wiele lepiej

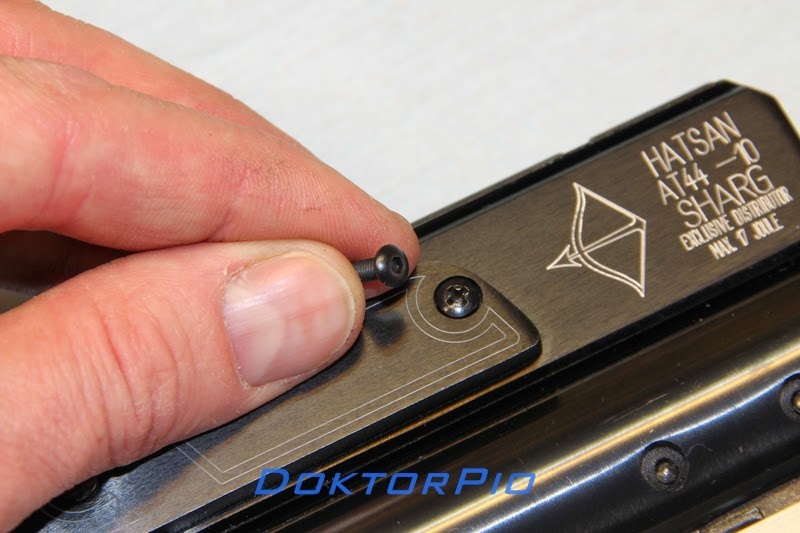
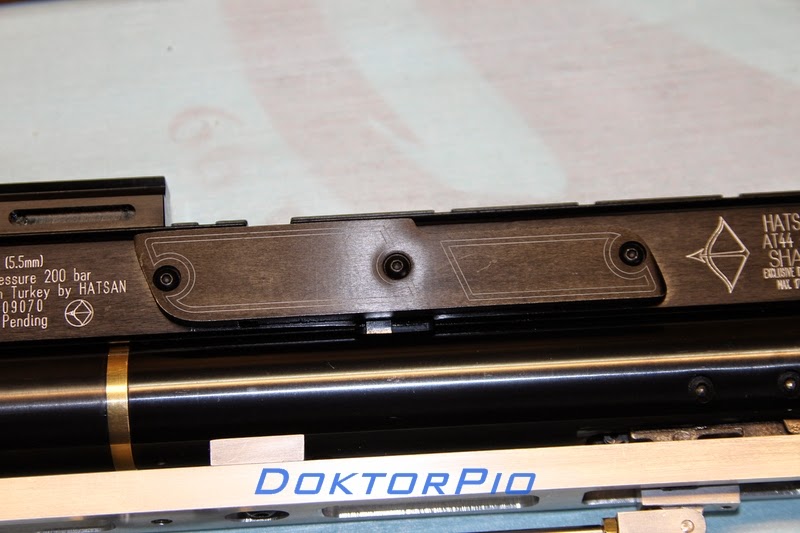
A na koniec wyfrezowany separatorek. Teraz to już koniec prac nad systemem czas się zabrać za wykonanie osady.
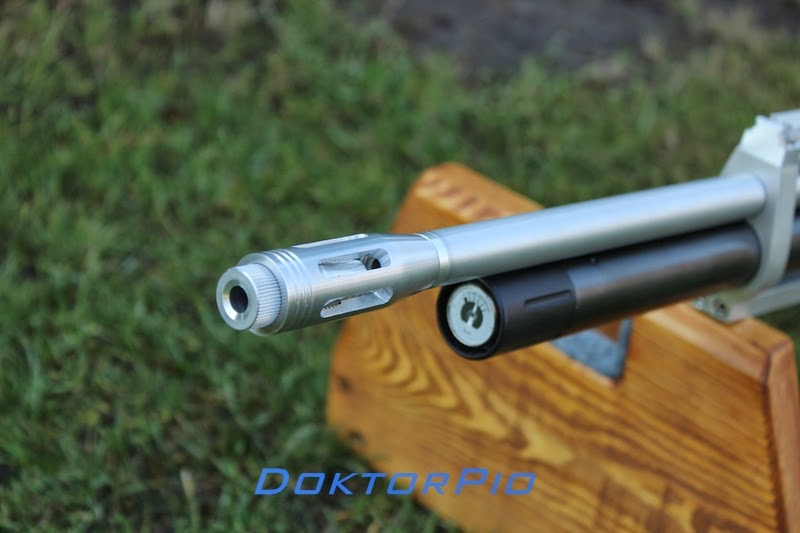
Osadę wykonam z drzewa jesionowego. Prawdę mówiąc było mi obojętne z jakiego rodzaju drzewa wykonam osadę bo ostateczne osada miała być pomalowana czarna farba strukturalną. W trakcie kolejnych etapów wykonywania osady osoby które ja widziały doradzały mi żebym nie malował osady na czarno tylko ładnie wykończył olejem.
Oto materiał na osadę.

Osadę zaprojektowałem a następnie wyciąłem w tekturze.
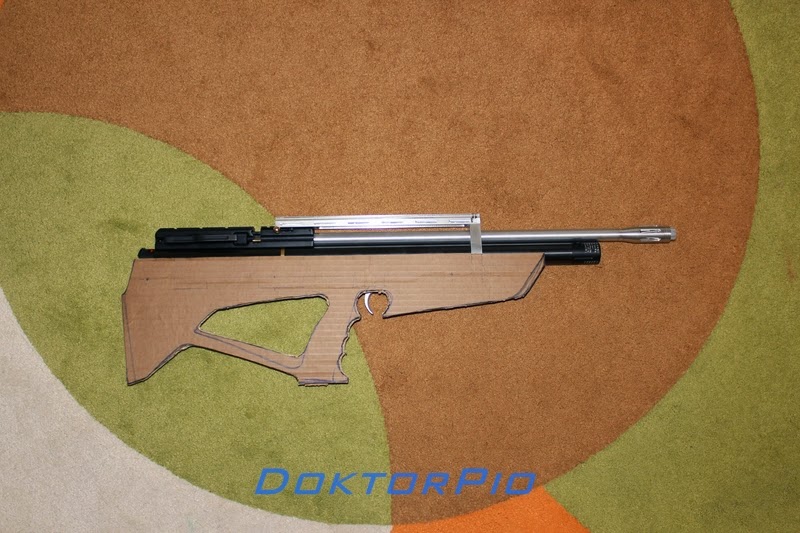
Na poczet wykonania osady musiałem kupić frezarkę do drewna. Na foto widać pierwsze frezowania.
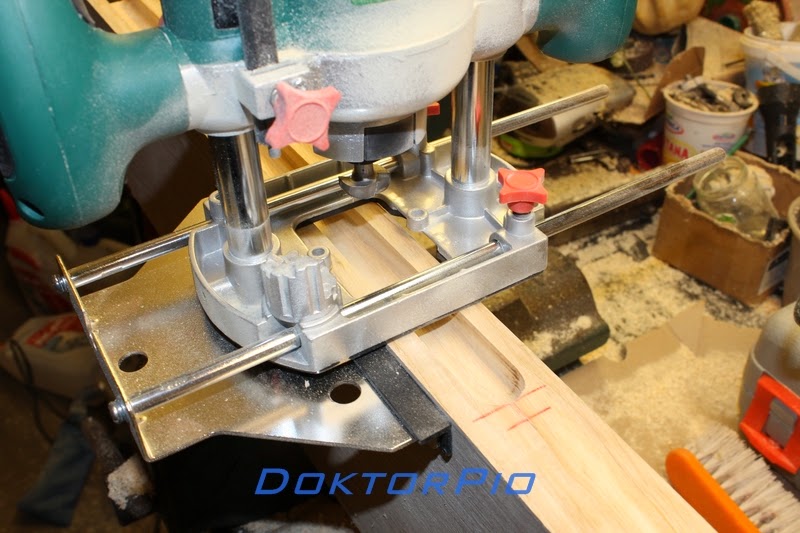
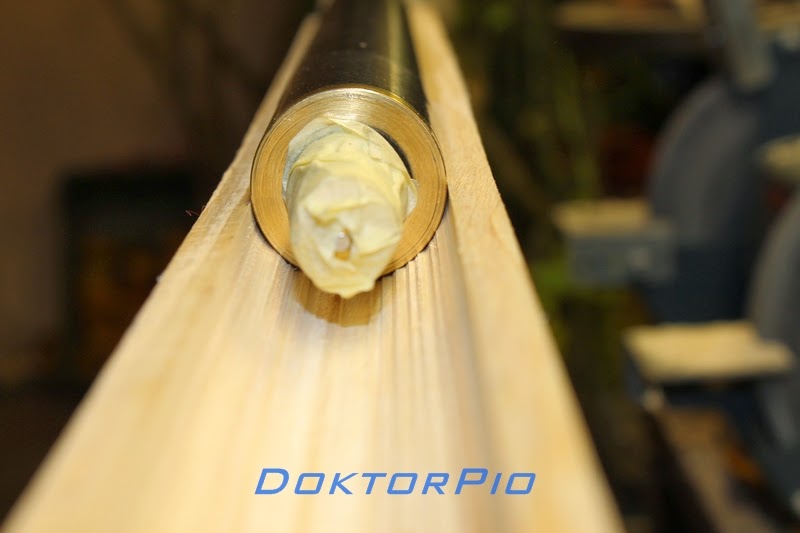
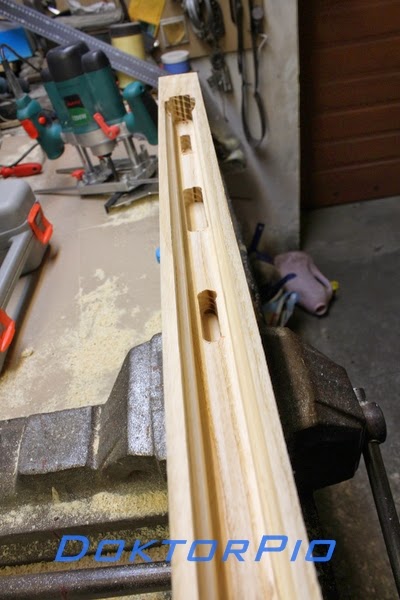
Pierwsze przymiarki systemu do osady


Szkic kształtu osady naniesiony na deskę. Oczywiście trzeba precyzyjnie nanieść miejsca gdzie będzie spust a także uchwyt itp.


Czas na wycinanie osady, najpierw na zakrętach wiercę otwory wiertłem do drzewa a następnie wycinam pilarką.


Pierwsze kształty i przymiarki do systemu


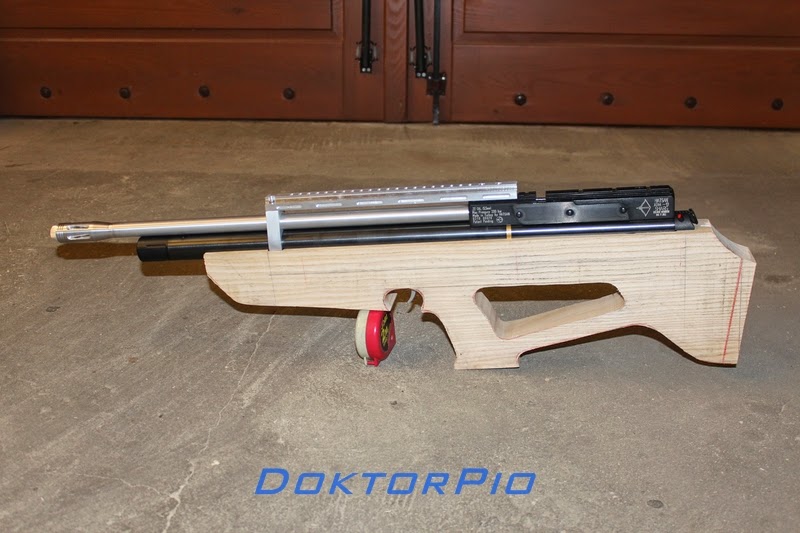
Kolejne etapy obróbki to frezowania boczne, użycie pilnika tarnika ręcznego oraz na wiertarce.
Szlifowanie powierzchni papierem ściernym o gradacji 60 -80 -120 -240 -320.
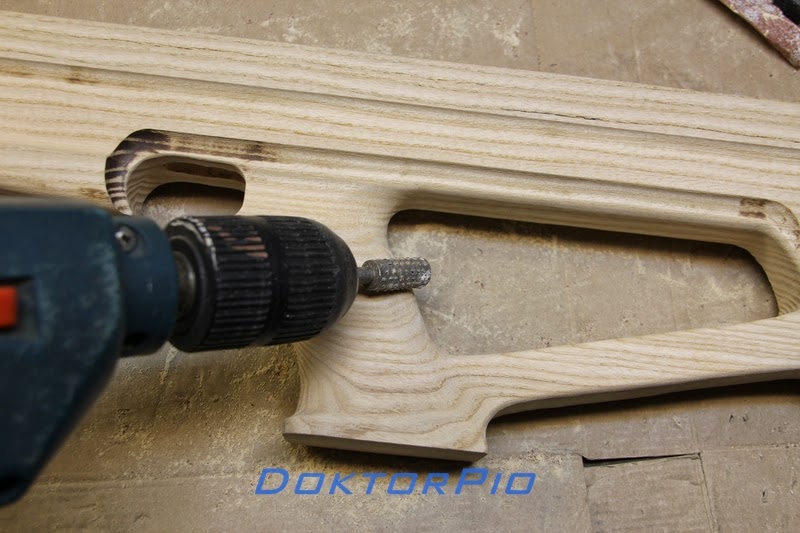
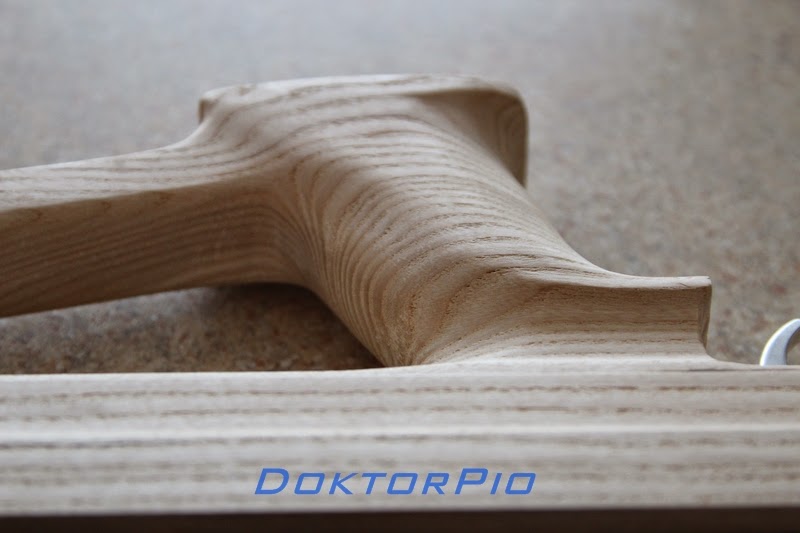


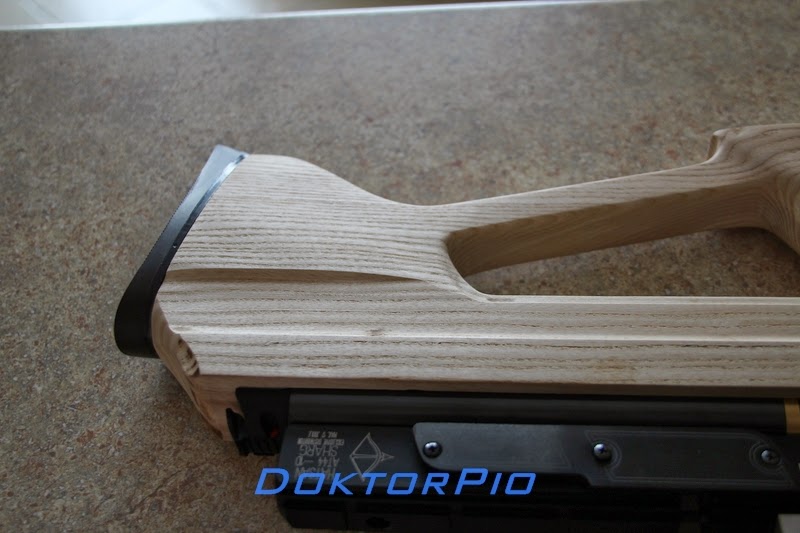
Dorobiłem osłonę cyngla spustu.

Dalsze etapy wykończenia osady to wygładzanie powierzchni drobnym papierem o gradacji 500. Przecieranie powierzchni wilgotną gąbka i ponowne docieranie. Kolejne prace to stosowanie waty stalowej 000.
Tak dla naznaczenia swojego produktu, wypaliłem na osadzie ploterem laserowym CO2 swoje logo

Gdy powierzchnia osady była już dla mnie satysfakcjonująca. Nałożyłem olej lniany + terpentyna + bejca następnie starcie benzyną ekstrakcyjną z powierzchni osady zastosowanej wcześniej mikstury to po to by bejca została tylko w słojach drewna. Kolejne warstwy to olej lniany+ terpentyna z coraz mniejsza ilością terpentyny aż do momentu zastosowania samego oleju lnianego :-D
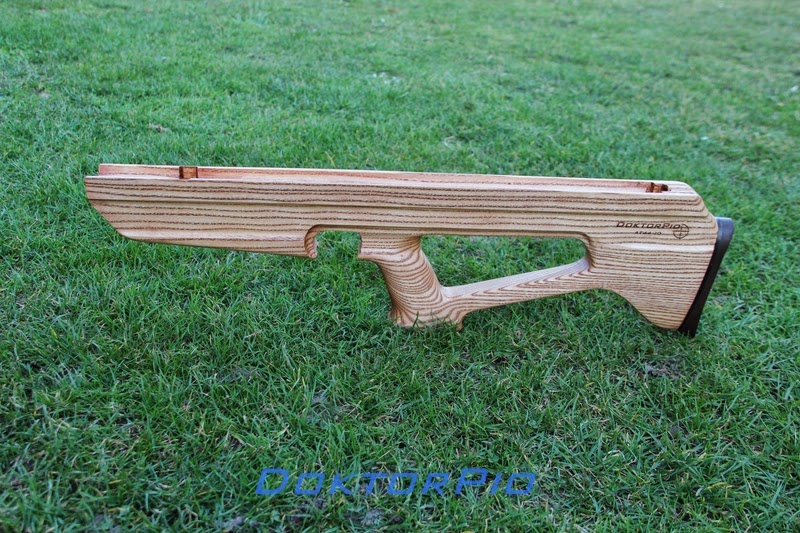
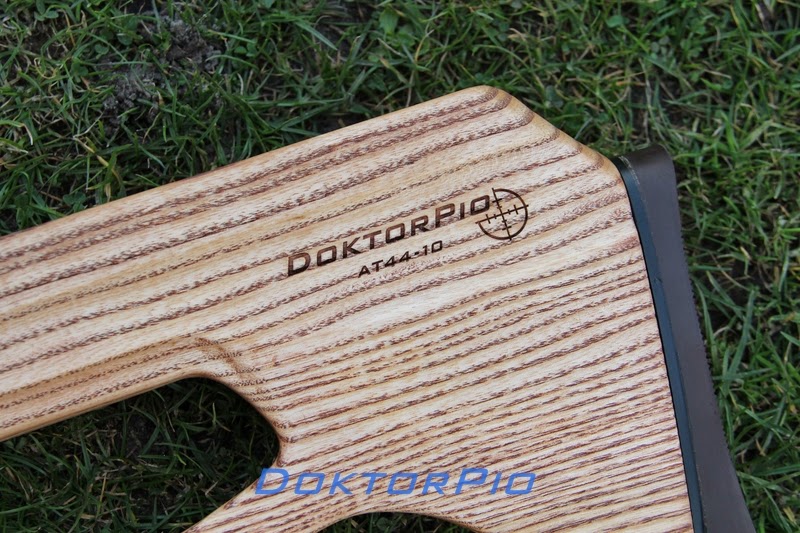


Wszystkie elementy karabinka tuż przed ostatecznym złożeniem.

A poniżej fotki gotowego Hatsan AT44-10 BULLPUP wersja DoktorPio

Wersja z separatorem i tłumikiem.
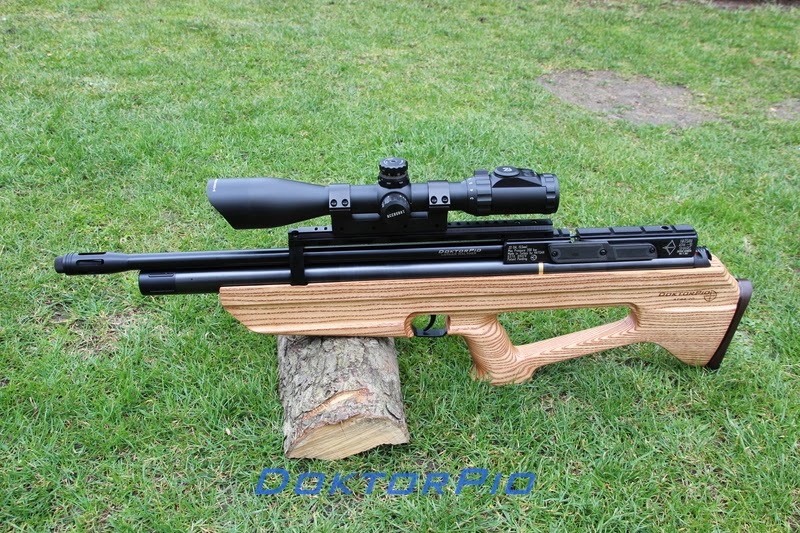

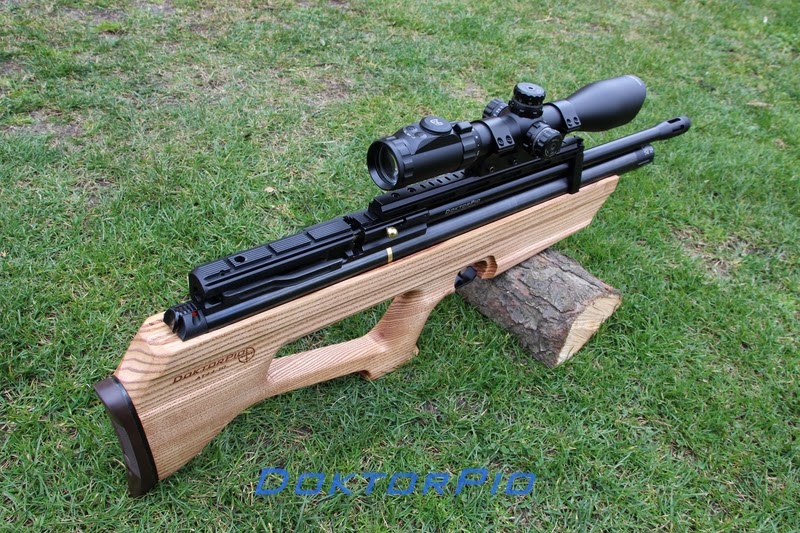
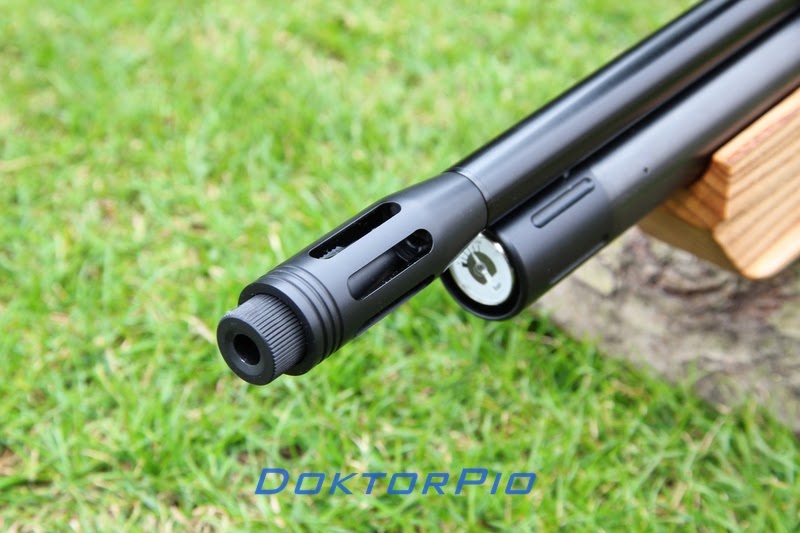
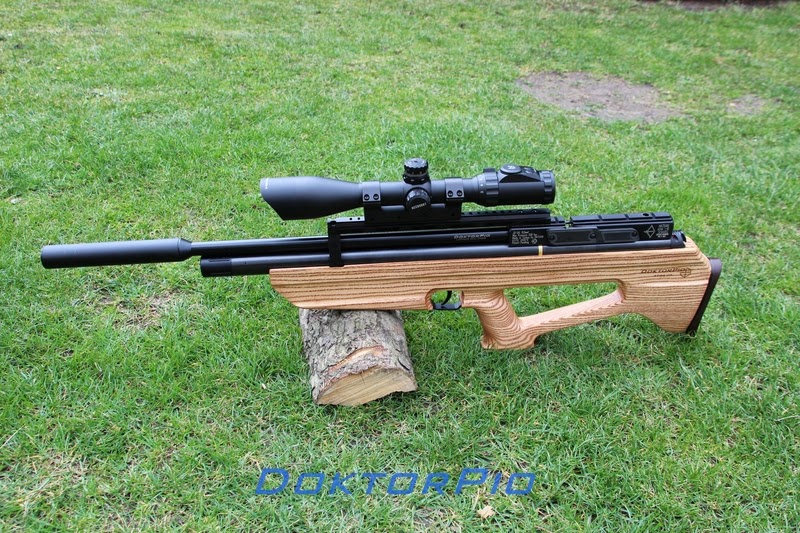
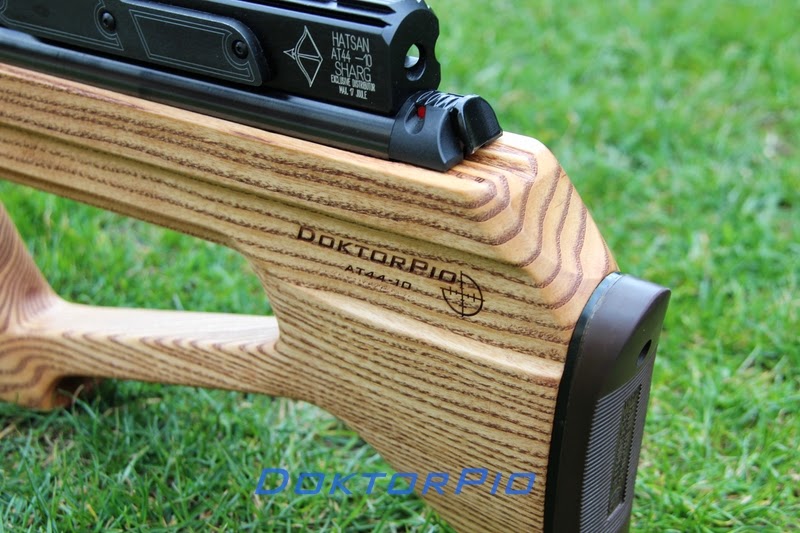
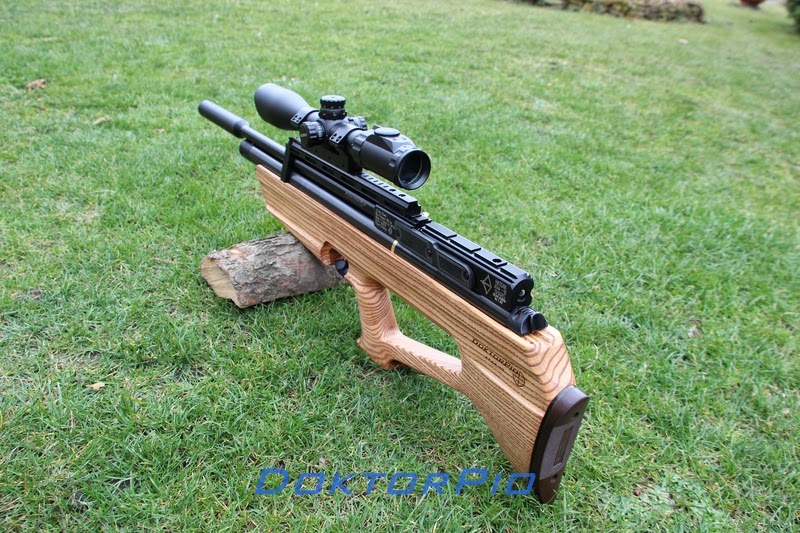
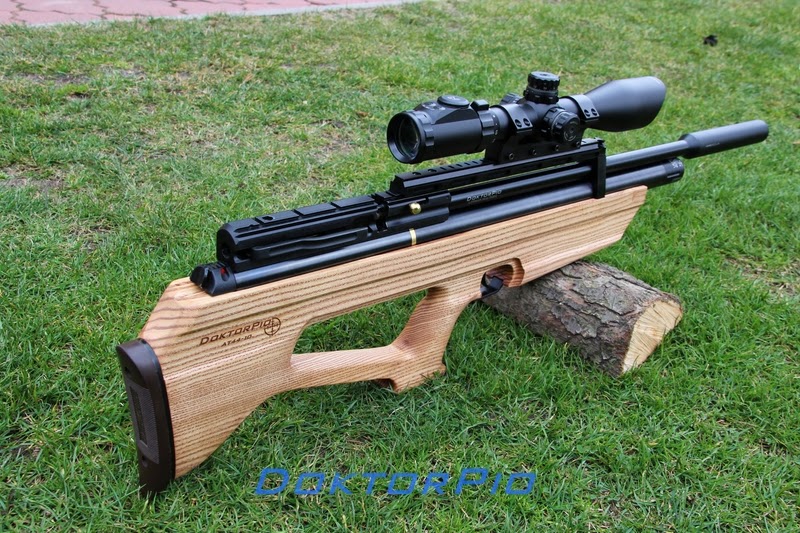
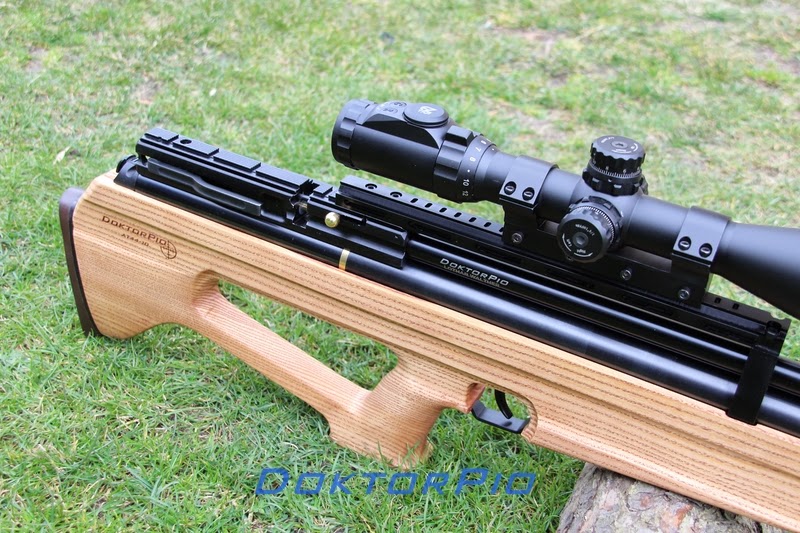
Logo na osłonie lufy również wykonane za pomocą plotera laserowego CO2

Fakt jest taki że dość długo zajęło mi zabranie się do tego projektu :-D To wszystko wina totalnego braku czasu. A ja jak się za coś biorę to lubię zrobić to coś perfekcyjnie i do końca a to jak wiadomo wymaga czasu. Kolejny problem to dostateczny brak dostępu do tokarki czy frezarki. Generalnie jestem bardzo zadowolony z efektów swojej pracy.
Karabinek w swojej budowie i konstrukcji jest dość krótki i zwarty przyjemnie składny robiony pod siebie :-D System przeładowania działa przyjemnie i miękko, spust jest wyczuwalny i przewidywalny z możliwością wyregulowania go pod swoje upodobania. Oczywiście spust nie działa tak jak w np. HW100 ale co tam :-D . Super się strzela z pozycji na stojaka z pozycji siedzącej lub z kolana, jak wiadomo karabinek tej kategorii jest super poręczny w przedzieraniu się przez trudny teren zarośla krzaki :-D
Dane techniczne:
-długość karabinka 72 cm
-długość z separatorem 78 cm
-waga samej osady 0,9 kg
-waga karabinka kompletnego z separatorem bez optyki 4,0 kg
Poniżej przedstawiam pierwsze wyniki strzelania na 50m pozycja siedząca.
Oczywiście wiem że może być lepiej ale to naprawdę były pierwsze strzelania, jeszcze muszę popracować nad pozycją uchwytem karabinka itp.
W wolnej chwili przedstawię wyniki strzelań w limicie na dalsze dystanse.
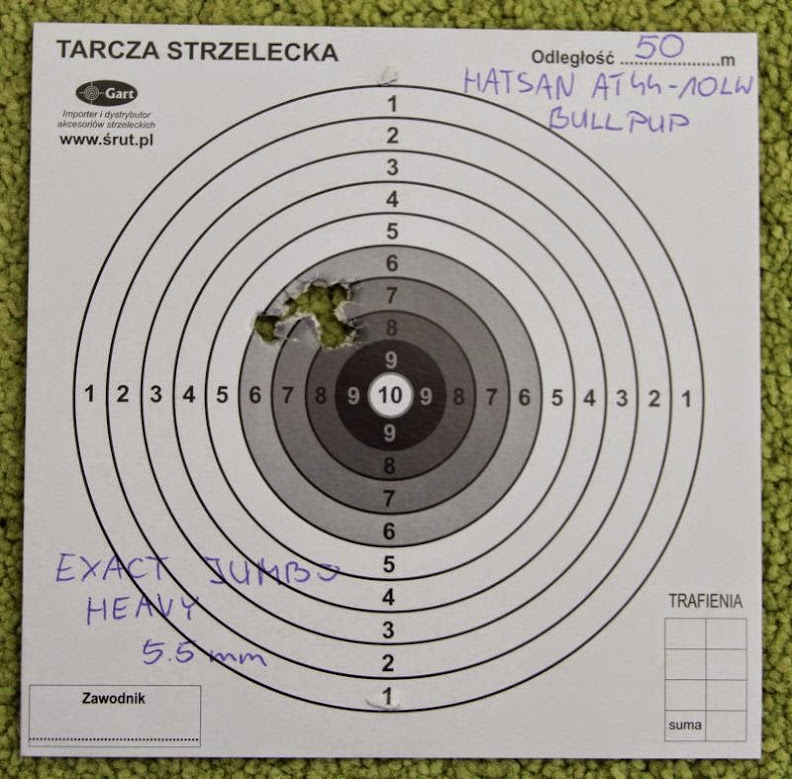
